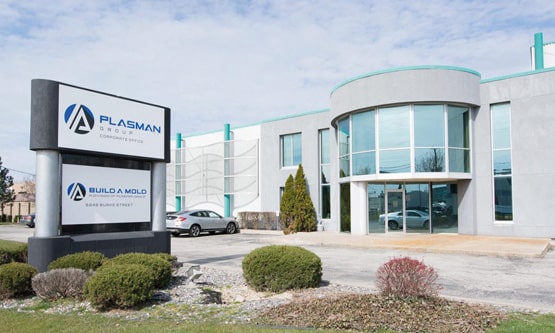
Windsor Tooling-Plasman Group, the world leader in automotive components, has chosen ONA EDM machines for its high precision and productivity.
Advantages of ONA EDM machines: High precision and productivity
Windsor Tooling-Plasman Group, the world leader in automotive components, has chosen ONA EDM machines for its high precision and productivity.
ONA has been at the forefront of virtually all important developments for electrical discharge machining. Throughout almost 70 years of experience, we have always been committed to investing in the future, which lead us to become the most specialized manufacturer worldwide. We have 15,000 machines installed in more than 60 countries, 98% overall equipment efficiency, and hundreds of satisfied customers with whom we have built lasting relationships based on trust.
For all these reasons, we are still chosen by companies like Windsor Tooling-Plasman Group (Canada), specialized in the manufacture of plastic injection molds for the automotive industry. The company started its activity in 1978 as a small mold workshop. The founder, Alec Pinsonneault, envisaged the industry’s changes and needs and, subsequently, bet strongly on expansion, creating the foundations of what today is PLASMAN GROUP, a world leader in automotive components (design applications, molds, paint, assembly, among others) with more than twelve manufacture plants in six countries: Canada, USA, Mexico, Belgium, Sweden, and Norway.
Windsor Tooling-Plasman Group has recently acquired four ONA EDM machines for its facilities in Windsor (Ontario), apart from the other three machines it already had (H600, H400 and PRIMA S900).
The four new pieces of equipment are:
Before choosing these machines, the company asked us and four other EDM manufacturers to carry out five electrical discharge machining tests. After getting the results, Windsor Tooling-Plasman Group finally chose us due to our “accuracy, excellent support and best speed“.
The TQX10 machine -the one with the largest dimensions on the market- has, in fact, a double head to perform machining operations in half the time. Simultaneous work at the right and left of the tank is also possible, separating it as if it were two independent machines. It is an ideal piece of equipment for the manufacture of large molds with different cavities. More than two decades ago, ONA became a pioneer in the development of this second head. Few manufacturers have access to this technology.
ONA, 15% faster than the best competitor.
The five different electrical discharge machining tests proposed by Windsor Tooling-Plasman Group (to us and the four competitors) had to be carried out on a single part. All the tests were performed in the presence of the customer. Our facilities in Durango (Spain) were visited by the EDM Manager and the Mold Maker Manager from Windsor Tooling-Plasman Group. We made the test using a QX8 machine.
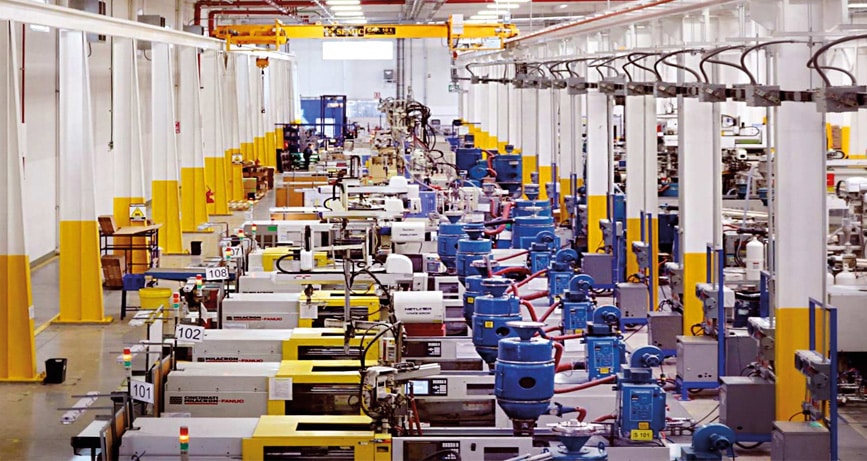
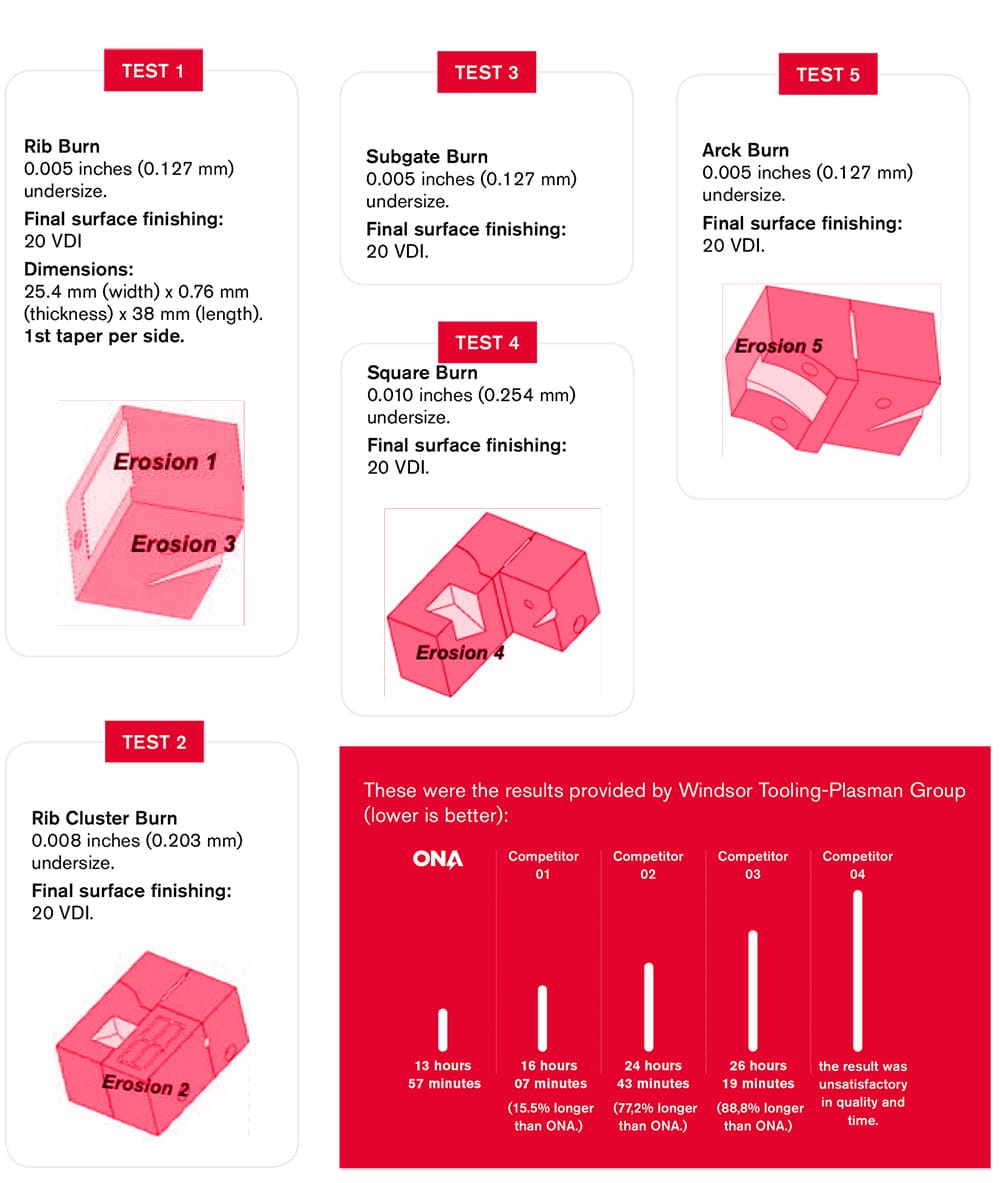
EDM for the machining of the largest turbine disc firtrees.
ONA’s WEDM technology has proven to be a match for conventional methods such as broaching and milling in terms of quality and precision
Dubral optimises the precision and quality of its cutting with ONA AV35 model
The acquisition of the ONA AV35 model has allowed the company to improve the precision in its cutting, increasing efficiency
Sermec acquires the ONA AV35 machine to strengthen its EDM machining capacity
This fleet currently includes 4 wire EDM machines (AF25, AF35, AV25 and AV35), as well as a DR2 model erosion drilling machine.
ONA EDM technology optimises the performance of the MCM production process
The acquisition of ONA’s AV25, AV35 and AV60 models has meant an increase in profitability and quality for MCM and a high level of satisfaction.
Sabacaucho to machine large moulds for elastomeric parts with the ONA IRIS8 B1L+ machine
Sabacaucho’s requirement for a machine with a high capacity for machining and repairing larger moulds led the company to contact ONA.
Tecnijusta expands its capacity to manufacture larger moulds with the ONA Iris 6 machine
Tecnijusta acquires the ONA Iris 6 model to strengthen its capabilities and improve efficiency in the EDM process.