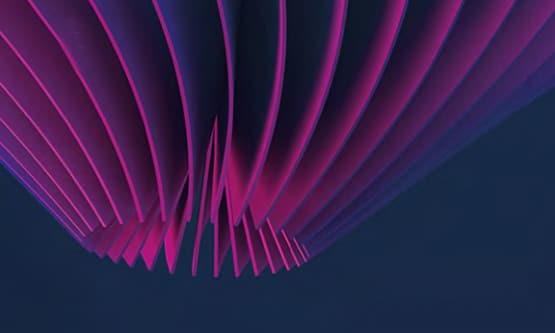
Pump and valve manufacturer trusts in ONA for the machining of turbine impellers with EDM for industrial compressors.
The machining of turbine impellers with EDM for industrial compressors
Two of ONA’s strengths in the turbine component manufacturing industry are based on our expertise in electrical discharge machining (EDM) of highly complex parts, as well as over 25 years of experience in providing turnkey solutions for the turbine industry.
This market leadership and expert knowledge is what has led one of the benchmark companies in the manufacture of pumps and valves to place its trust in ONA to develop the turbine impellers for its rotary equipment.
EDM is the most efficient and viable option for machining parts with complicated geometries, such as impeller cavities. This is due to the fact that EDM technology overcomes the difficulties presented by other traditional techniques, such as milling, which often leads to high tool breakage rates or, especially in the case of closed or complex geometries such as impellers, the impossibility of the milling tools to reach all areas to be machined.
However, while electrical discharge machining is the most feasible method to provide an optimum erosion and machining solution, it also poses major challenges: EDM involves taking into account several complicated factors, such as design and number of necessary electrodes, their trajectory, level of wear, etc., the calculation and definition of which must be carefully considered.
To meet these challenges, our engineering team developed a “turnkey solution” that addressed all the needs given by the client. To this end, it studied and assessed the specific case in detail, successfully developing the tailor-made application for machining the impellers, the ‘heart’ of the turbines, that would be used by our client for generating power, pumping and moving fluids industrial compressors.
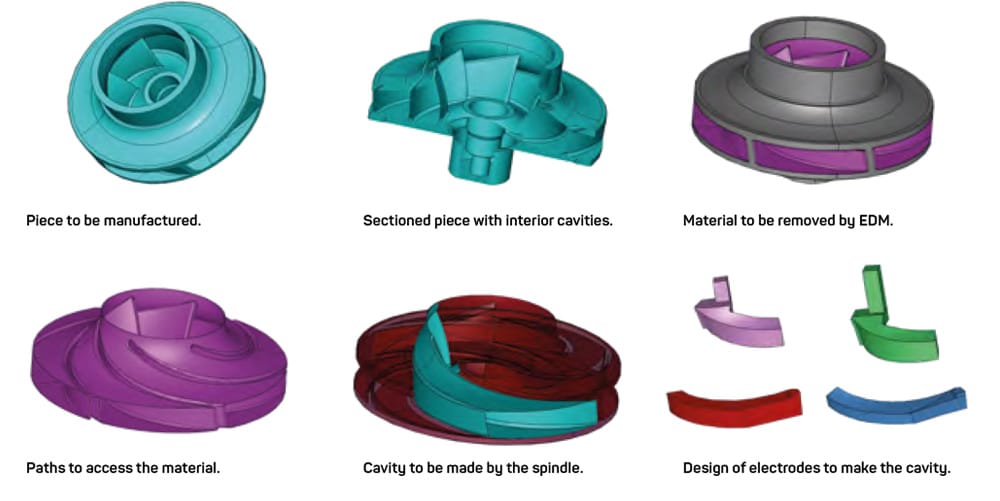
How we managed to do it
Based on the drawings provided by the customer and the needs expressed, ONA’s team assessed the suitability of using die sinking EDM technology in the machining of geometrically complicated parts such as the impellers.
1. Layout
In this initial phase, it was essential to correctly define the axis involved in the process, as well as the position and orientation of the workpiece, since both factors significantly affect electrode design and trajectory, machining size and may even compromise the viability of the project itself.
2. Electrode design and trajectory
Currently, no commercial CAD/CAM software is available on the market that is capable of determining electrode design and trajectory as in the case of other applications, meaning expert knowledge must be drawn upon to develop ad hoc algorithms and methodologies to define such parameters. This means there is no single solution, but each workpiece requires a customised project according to its particular characteristics and needs.
3. Electrode machining
The challenges of machining and milling the electrodes themselves mainly have to do with their complex geometries and the need for very tight tolerances; this means that an error in the electrode leads to an error in the workpiece.
4. EDM parameters
For stable machining of the workpiece, the different EDM parameters must be correctly defined. These parameters are mainly defined by the required surface roughness (the shorter the machining time, the higher the roughness) and geometry (larger areas allow more energy to be applied).
5. Electrode wear
Wear is an unavoidable consequence of the EDM process; it cannot be prevented but it can be controlled and minimised.
6. Metrology
Given the difficulty to access the part itself, the dimensional analysis of the part in question is a challenge in itself; so methods like destructive analysis, defining strategic points or using standard measurement elements are some of the possibilities to be considered here.
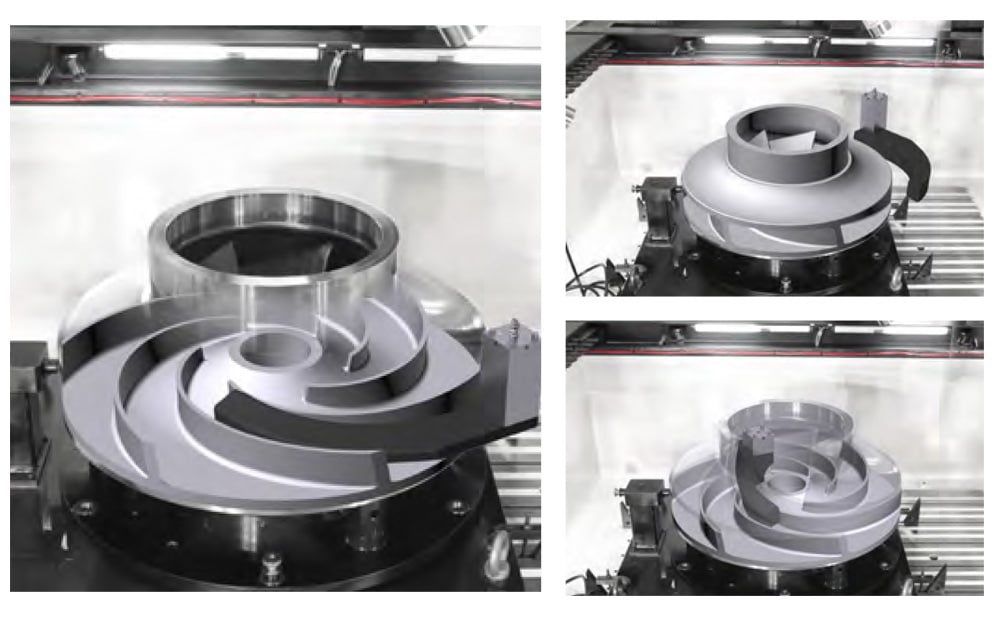
ONA’S SOLUTION: how we came up with it
In order to successfully overcome all the challenges involved in this project, it was essential to employ a team of engineers such as ONA’s, experts in EDM technology.
After an in-depth preliminary study of the workpiece and its different parameters, and following an assessment of the feasibility of the project, our engineers’ proposal was to develop an application for our IRIS 6+ die sinking EDM machine. This equipment, among other advantages, offers maximum EDM precision and high productivity levels
In addition to choosing the most suitable machinery, ONA’s comprehensive development of the final application included critical parameters such as the definition of the required electrodes and analysis of their wear. In the case of this project, the application required 4 different electrodes to achieve full trajectories. This is also one of ONA’s competitive advantages in terms of time optimisation. Although eventual electrode wear is inevitable, the technology built into ONA IRIS’s 100% smart digital generator reuses the electrodes and reduces their wear.
Likewise, the team of engineers developed the three-dimensional trajectory (curves, inclinations…) that our machine has to follow so that the whole process is correctly executed, and, where necessary, a customised clamping tool was implemented to correctly position the part.
Conclusions
- ONA proves its capacity to tackle integral turnkey projects.
- Development of a customised application for the manufacture of a highly complex part in terms of shape, access and cavities.
- Clear example of technological potential and EDM expertise.
- Precision and reliability of IRIS machines for the machining of critical, complex parts.
- ONA as a technology partner specialising in sectors such as the manufacture of turbine components. In this particular case, the focus is on the machining of impellers, but here you can read about another case study regarding our customised solution for the machining of diffuser bores in turbine blades.
EDM for the machining of the largest turbine disc firtrees.
ONA’s WEDM technology has proven to be a match for conventional methods such as broaching and milling in terms of quality and precision
Dubral optimises the precision and quality of its cutting with ONA AV35 model
The acquisition of the ONA AV35 model has allowed the company to improve the precision in its cutting, increasing efficiency
Sermec acquires the ONA AV35 machine to strengthen its EDM machining capacity
This fleet currently includes 4 wire EDM machines (AF25, AF35, AV25 and AV35), as well as a DR2 model erosion drilling machine.
ONA EDM technology optimises the performance of the MCM production process
The acquisition of ONA’s AV25, AV35 and AV60 models has meant an increase in profitability and quality for MCM and a high level of satisfaction.
Sabacaucho to machine large moulds for elastomeric parts with the ONA IRIS8 B1L+ machine
Sabacaucho’s requirement for a machine with a high capacity for machining and repairing larger moulds led the company to contact ONA.
Tecnijusta expands its capacity to manufacture larger moulds with the ONA Iris 6 machine
Tecnijusta acquires the ONA Iris 6 model to strengthen its capabilities and improve efficiency in the EDM process.