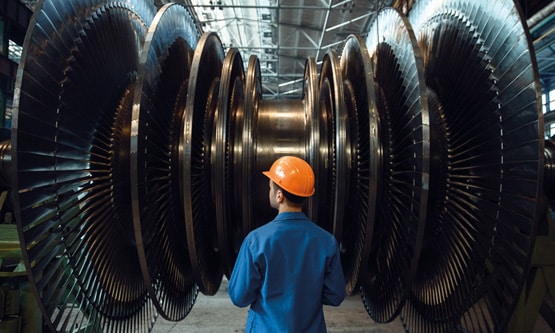
Gas turbine manufacturers trust in ONA AV35 wire-cut model as the perfect EDM solution for turbine disc firtree production.
ONA AV35 wire-cut model, EDM solution for turbine disc firtree production
Presently, ONA has the highest expertise in the world as EDM machine-tool manufacturer. Years of experience in the field together with advanced technology focus in providing customized solutions to its customers, position ONA as preferred EDM equipment supplier for a major industrial gas turbine OEM, which is part of a much-admired technology corporation that provides products and services for aerospace, aviation, healthcare, power generation, renewable energy, digital industry, additive manufacturing, venture capital and finance.
ONA AV35, perfect for turbine disc firtree production.
AV35 incorporates the latest wire EDM technology required for high-end critical parts such as the turbine discs and blades. That’s why standard AV35 has been customized with complete apparatus and accessories to be used to wire EDM machine turbine discs firtree. In other case, same standard AV35 has been slightly modified such as to be used to cut larger blades and that way saving money and floor space for purchasing a larger machine. This proofs that ONA EDM finds ways to adapt its machines to the customer needs, creating fully configurable products.
With a robust and compact design, ONA AV35 has high industry reliability standards, and as the rest of the wire EDM equals profitability thanks to:
- High-efficiency and low-consumption generator.
- Optimized filtration system using cycles and puReduced consumable costs.
- EDM technology including wire low consumption.mps settings that save energy.
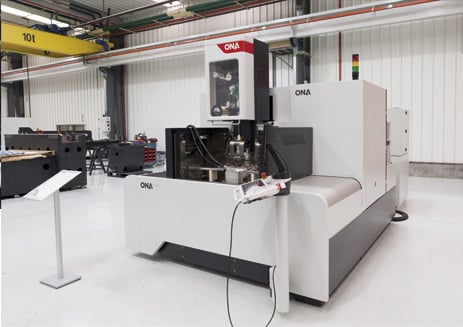
In addition to that, in some cases, the machining process can be fully automated. A continuous information exchange between machine and the production facility industrial environment allows better process control, less interruptions and implicitly longer hours of continuous machine operation. Any deviation from the initial process setup can be monitored in real-time and decisions can be made right away. For example, if the dielectric temperature gets out of the programmed limits an alarm pops up. All this translates into higher productivity.
After the customer’s acquisition of the first four AV35 machines, more machines were required to cope with an increased production volume. The undoubtable performance and reliability of the first four AV35 machines have triggered the acquisition of another four, getting to a total amazing number of eight AV35 installed machines in less than 1 year span.
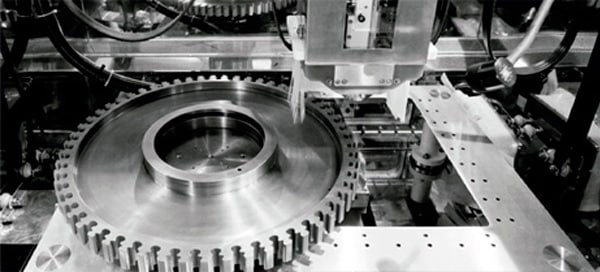
The total EDM production capacity consists of:
- \ 4 AV35 wire EDM (2020)
- \ 4 QX4 die-sinking EDM (2020)
- \ 4 AV35 wire EDM (2019)
- \ 1TQX8 double-head die-sinking EDM (2016).
- \ 2 TX8 double-head die-sinking EDM (2013, 2015)
- \ 1 NX6 die-sinking EDM (2013)
The combined accuracy and cutting speed are the main reasons for which ONA was entrusted for such complex EDM projects within long-term relationship.
EDM for the machining of the largest turbine disc firtrees.
ONA’s WEDM technology has proven to be a match for conventional methods such as broaching and milling in terms of quality and precision
Dubral optimises the precision and quality of its cutting with ONA AV35 model
The acquisition of the ONA AV35 model has allowed the company to improve the precision in its cutting, increasing efficiency
Sermec acquires the ONA AV35 machine to strengthen its EDM machining capacity
This fleet currently includes 4 wire EDM machines (AF25, AF35, AV25 and AV35), as well as a DR2 model erosion drilling machine.
ONA EDM technology optimises the performance of the MCM production process
The acquisition of ONA’s AV25, AV35 and AV60 models has meant an increase in profitability and quality for MCM and a high level of satisfaction.
Sabacaucho to machine large moulds for elastomeric parts with the ONA IRIS8 B1L+ machine
Sabacaucho’s requirement for a machine with a high capacity for machining and repairing larger moulds led the company to contact ONA.
Tecnijusta expands its capacity to manufacture larger moulds with the ONA Iris 6 machine
Tecnijusta acquires the ONA Iris 6 model to strengthen its capabilities and improve efficiency in the EDM process.