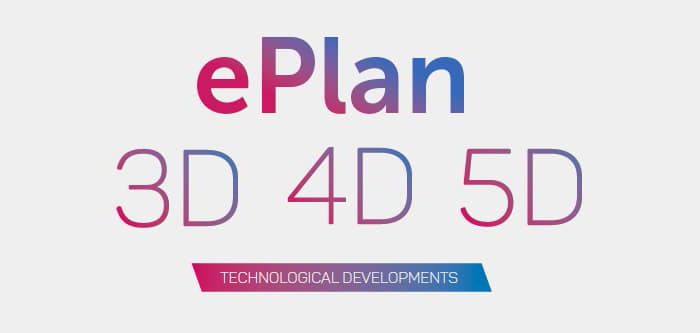
Innovation in the design of the ONA Halley model, the digital native machine
Innovation in the design of the ONA Halley model, the digital native machine
In the field of design and manufacture of industrial machines, it is essential to have efficient and precise tools to ensure a smooth and high-quality process.
In this context, the ePlan engineering program is a complete and flexible solution that optimises all stages of development. One of the outstanding innovations in ePlan is the replacement of traditional technical drawings with 3D models of the machine. At ONA, the implementation of this new design methodology has led to an evolution of the traditional system, incorporating new dimensions into the project that previously did not interact with the model.
These dimensions provide the ability to access model data and process it in conjunction with other workflows and processes that are directly related. In this way, it impacts directly on the budgets, the programming, the operation and the logistics, which allows savings in time and costs and increases the quality of the machine.
3D
Three-dimensional model
- Graphic description
- Geometric info.
- Project visualisation
- Objects with properties and attributes etc.
4D
Programming
- Simulation of project phases
- Simulation of assembly
- Execution plan design
5D
Cost control
- Conceptual model in real time
- Cost estimation
- Material lists
- Prefabrication solutions
Special tools for each stage of the process
The entire ePlan ecosystem is made up of three main tools, each focused on a specific stage of the design process:
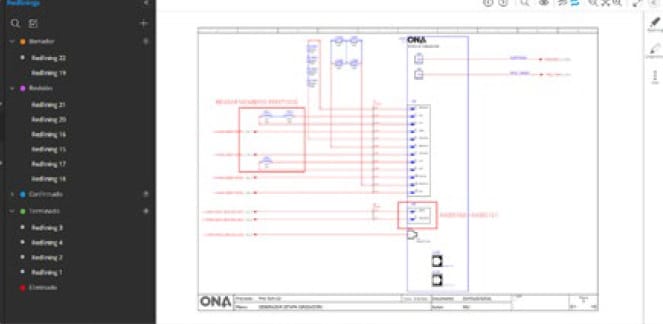
ePlan P8 eléctric:
This tool takes care of the design of the electrical components, generating the electrical diagrams based on the technical and functional specifications of the machine to be built, such as the ONA HALLEY model. Lists of materials are created for the electrical cabinet, the wiring is specified, the connection of the components is designed, and the power and handling-control system is developed. This stage establishes the database that will be used in the following phases of the process.
ePlan P8 eléctric:
In the second stage, the control cabinet and internal wiring are designed and modelled in a 3D environment. Information from the previous stage is used to accurately size and model the cabinet. Two-way communication is established with the previous stage to create a list of components to be fitted in the cabinet, avoiding the loss of information. The level of detail of the modelling at this stage makes it possible to solve problems of space and assembly in the design itself, which reduces costs in the final stage of production. Also worth noting is the use of a new system from the manufacturer Lutze, which replaces the classic mounting plate with a system without ducts and with a rear natural ventilation space, optimising the space used and prolonging the useful life of the components.
ePlan Pro Panel:
The third tool in the ecosystem is responsible for the design and modeling of the machine’s external wiring. Using the documentation generated in earlier stages and the 3D model of the machine, the external wiring is specified, routed, and connected to the corresponding components. A complete 3D model is created with detailed information about the wiring and its specifications (assemblies, connectors, connections, dimensions, and cable routes). This model provides a clear visualization of the cables according to their function, which facilitates installation and maintenance.
These three tools communicate and constantly update documentation and models at all stages of the process. This two-way communication guarantees the traceability of the information and the coherence of the design in all phases, thus facilitating the exchange of information between the different project agents.
Finally, the fourth stage of the process is the installation of the machine. This stage involves the use of a tablet as a viewer and the following tools and reports:
An ePlan tool called eCloud:
This is used to view and make changes to electrical diagrams. The assemblers can visualise and record the necessary modifications in real time, instantly transmitting them to the responsible design technicians.
ePlan Harness reports:
Automatic reports are generated that include wiring specifications (measurements, stripped ends, pins, connectors, etc.). These reports facilitate the preparation and organisation of the necessary cables for the installation.
ePlan Harness 3D model:
The 3D model is used to visualise cable routing and component layout, allowing for precise component placement and a clear visualisation of the machine set-up.
Together, these tools and resources from the ePlan ecosystem provide a comprehensive solution for the design and installation of machinery, improving efficiency, the quality of the documentation generated and traceability throughout the machinery development cycle.
ePlan ecosystem:
The electric evolution of the ONA HALLEY model
The ePlan ecosystem has been implemented in the construction and generation of electrical documentation for the new ONA HALLEY model. This methodology will include advanced designs and more accurate documentation, resulting in better performance and efficiency for the model by adding new dimensions. In addition, it will become the new standard methodology for the construction and generation of documentation for all ONA machines in the future.
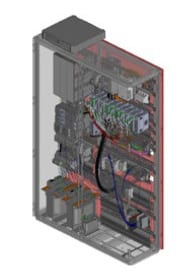
EDM for the machining of the largest turbine disc firtrees.
ONA’s WEDM technology has proven to be a match for conventional methods such as broaching and milling in terms of quality and precision
Dubral optimises the precision and quality of its cutting with ONA AV35 model
The acquisition of the ONA AV35 model has allowed the company to improve the precision in its cutting, increasing efficiency
Sermec acquires the ONA AV35 machine to strengthen its EDM machining capacity
This fleet currently includes 4 wire EDM machines (AF25, AF35, AV25 and AV35), as well as a DR2 model erosion drilling machine.
ONA EDM technology optimises the performance of the MCM production process
The acquisition of ONA’s AV25, AV35 and AV60 models has meant an increase in profitability and quality for MCM and a high level of satisfaction.
Sabacaucho to machine large moulds for elastomeric parts with the ONA IRIS8 B1L+ machine
Sabacaucho’s requirement for a machine with a high capacity for machining and repairing larger moulds led the company to contact ONA.
Tecnijusta expands its capacity to manufacture larger moulds with the ONA Iris 6 machine
Tecnijusta acquires the ONA Iris 6 model to strengthen its capabilities and improve efficiency in the EDM process.