AarKel achieves new levels of excellence in EDM machining with ONA.
AarKel achieves new levels of excellence in EDM machining with ONA.
AarKel has succeeded in standing out in EDM machining thanks to the collaboration with ONA. The installation of the ONA QX8 and ONA IRIS T10 C2 models has resulted in significant improvements, such as a 30% reduction in machining time, a notable improvement in product finishing, and a 50% reduction in manufacturing time. This successful collaboration demonstrates that having a trusted EDM supplier is critical to achieving excellence in the industry.
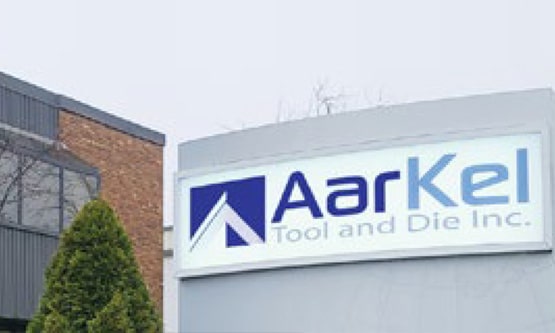
Successful collaboration with ONA
The company, with headquarters in Canada, faced specific challenges in EDM machining, especially when creating very small, highly detailed slots in plastic parts, as well as vehicle electrification and weight reduction in cast parts with deep traction grooves. In this search for solutions, the strategic collaboration with ONA has been essential. ONA, a well-known and trusted supplier in the industry, offered not only high quality and efficient EDM machines, but also exceptional service and support.
Notable achievements and benefits
The installation of the ONA QX8 and ONA IRIS T10 C2 equipment has generated significant improvements in the AarKel manufacturing process:
- A 30% improvement in EDM machining time, which has increased the efficiency of the process.
- The finish of the products has improved significantly thanks to th e improvements implemented.
- The introduction of the double head has made it possible to reduce manufacturing time by up to 50% compared to the previous process.
- Productivity has been optimised and has led to greater efficie ncy in the mould manufacturing process.
The power of the double head: ONA IRIS T10 C2
The ONA IRIS T10 C2 model, equipped with two simultaneous work heads, has been a key component in AarKel’s success. This innovative feature allows larger moulds to be finished in half the time, resulting in faster deliveries without sacrificing quality and precision. “We are seeing a 30% improvement in our EDM machining time, along with a better finish. When we use the double head, we cut up to 50% of the time that we used to spend in the manufacturing process before,” confirms the company’s president, Larry Delaey.
Thanks to the trust placed in ONA and its collaborative approach, AarKel has succeeded in improving the efficiency and quality standards in its manufacturing process. The installation of the ONA IRIS T10 C2 model with double heads has been a key to increasing productivity and providing shorter delivery times, without compromising excellence in the mould manufacturing process. AarKel has established itself as a leading company in the industry, ready to face any challenge in a constantly evolving market.
Outstanding features of the ONA IRIS T10 C2
- Two 132-position electrode changers with radio frequency identification (RFID), improving the management of production processes.
- Automated ecological filter to protect the environment.
- Powerful CNC capable of controlling up to 8 axes at the same time and of eroding in 3D without limitations.
- Independent work of the two heads, allowing the erosion of two cavities simultaneously in a single work piece.
- Automatic adjustment system for the dielectric level according to the erosion position of the head.
- Software specially developed for double head machines, maximising their performance and efficiency.