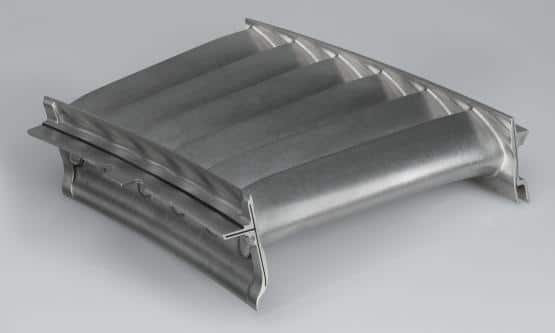
ITP trusts on the power of 12 die sinking ONA EDM machines for the erosion of the strip seal slots in the NGV segments of low pressure turbines (LPT)
EDM for the manufacture of strip seal slots in NGV segments
Industria de Turbo Propulsores S.A. (ITP) – a leader in engineering, research and development, manufacturing and casting, assembly and testing of aeronautical engines and gas turbines – trusts in the power of 12 die sinking EDM machines to erode the strip seal slots in the NGV segments of low-pressure turbines.
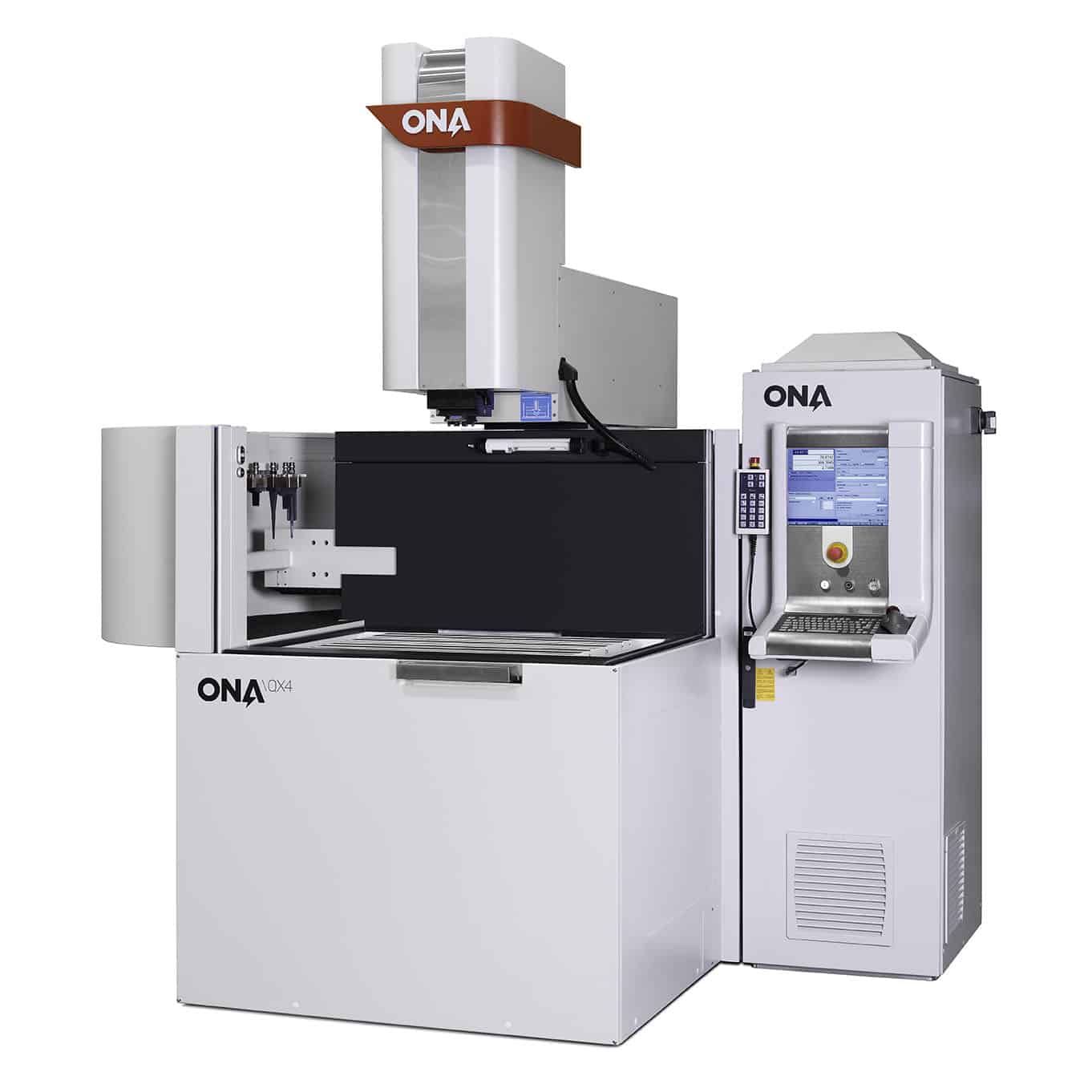
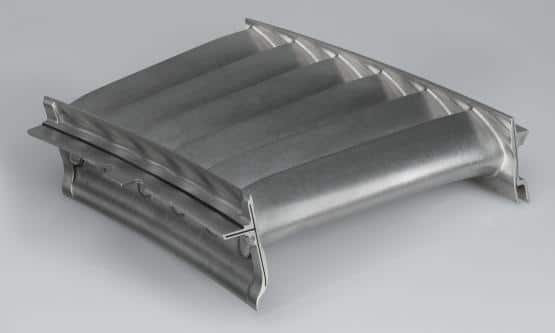
An NGV segment. The turbines consist of several stages of NGVs and blades. Each stage of NGVs is made up of between 18 and 38 NGV segments.
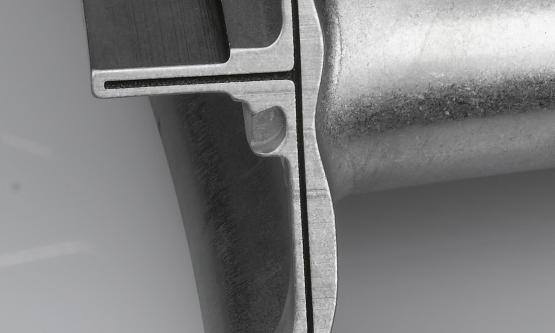
Detail of the slots (strip seal slots) machined by EDM in an NGV segment.
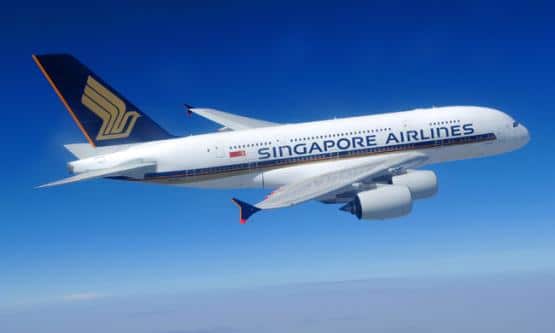
ITP has exclusively designed and manufactured the low pressure turbine for the Rolls Royce Trent 900 engine used in the Airbus A380, which is the world’s largest passenger aircraft, and the Trent 1000 that is used in the Boeing 787 Dreamliner.
EROSION OF THE STRIP SEAL SLOTS IN THE NGV SEGMENTS OF LOW PRESSURE TURBINES (LPT)
The initials NGV stand for ‘Nozzle Guide Vane’. Its purpose is to set up and redirect the flow of gas so that it strikes the moving blades in the best possible conditions for work to take place. Low pressure turbines have several stages of NGVs and blades. Each set of NGVs consists of between 18 and 38 NGV segments which are mounted in the engine in rings. To maintain the seal between the different segments, the lateral faces of the segments (wedge faces) have slots (strip seal slots) where strips can be inserted to produce a labyrinth seal. These strip seal slots are machined using EDM.
Erosion de las strip seal slots:
- The strip seal slots have different shapes and depths depending on the stage where they are located, but they can essentially be summarised in the following table:
- Component material: nickel based alloys.
- Depth: from 3.50 to 5.50 mm.
- Width: 0.74 +/- 0.10 mm.
- Cross section: from 40 to 80 mm2.
- Other: high precision requirements in the bottom radius.
- Electrode material: ultra-fine graphite.
Company:
Industria de Turbo Propulsores S.A. (ITP)
Employees:
3.000
Address:
Headquarters: Zamudio – Bizkaia – Spain. The ITP group has 17 centres located in Europe, America and Asia.
Activity:
ITP is a leader in engineering, research and development, manufacturing and casting, and the assembly and testing of aeronautical engines and gas turbines. ITP is the official maintenance service provider for most of the current aircraft engine manufacturers in the world. Sener Aeronáutica (53.12%) and Rolls Royce Aviation (46.87%) are shareholders in the ITP Group.
Turnover 2014:
EUR 650 million.
Customers:
Major manufacturers in the aeronautical sector (Rolls Royce, Honeywell, Pratt & Whitney, Eurojet…)
Equipment:
Die sinking EDM equipment for manufacturing NGVs at the production plant in Zamudio (Spain): 12 ONA die-sinking EDM machines.
Sabacaucho to machine large moulds for elastomeric parts with the ONA IRIS8 B1L+ machine
Sabacaucho’s requirement for a machine with a high capacity for machining and repairing larger moulds led the company to contact ONA.
Tecnijusta expands its capacity to manufacture larger moulds with the ONA Iris 6 machine
Tecnijusta acquires the ONA Iris 6 model to strengthen its capabilities and improve efficiency in the EDM process.
EDM for the machining of the largest turbine disc firtrees.
ONA’s WEDM technology has proven to be a match for conventional methods such as broaching and milling in terms of quality and precision
Dubral optimises the precision and quality of its cutting with ONA AV35 model
The acquisition of the ONA AV35 model has allowed the company to improve the precision in its cutting, increasing efficiency
Sermec acquires the ONA AV35 machine to strengthen its EDM machining capacity
This fleet currently includes 4 wire EDM machines (AF25, AF35, AV25 and AV35), as well as a DR2 model erosion drilling machine.
ONA EDM technology optimises the performance of the MCM production process
The acquisition of ONA’s AV25, AV35 and AV60 models has meant an increase in profitability and quality for MCM and a high level of satisfaction.