“ONA, the broadest experience and widest product range in EDM.”
INTERVIEW WITH PEDRO ECHENAGUSIA, PROJECT DIRECTOR AT ONA
\ “ONA, the broadest experience and widest product range in EDM.”
ONA’s specialisation as a manufacturer of large EDM machines is the result of the company’s natural evolution and strategic commitment. This is what ONA’s Project Director, Pedro Echenagusia, points out in this interesting interview.
This specialisation has earned the company international recognition and has positioned it as one of the world’s leading manufacturers of this type of machine, which is becoming increasingly important due to its major advantages over other traditional machining techniques such as broaching and milling.
Throughout its long track record in the manufacture of this type of equipment, ONA has had great success and overcome many difficulties, striving to respond to new customer needs and perfecting the structure and performance of its machines. Today, it continues to push forward, focusing on one main objective: “To improve customer satisfaction and strengthen customer relationships”.
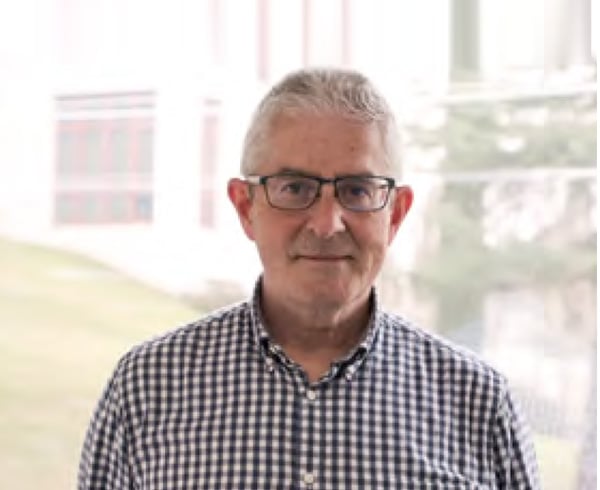
QUESTION. What are large machines? What are large machines considered to be?
ANSWER. In the case of die sinking EDM equipment, our models are the IRIS7, 8, 9 and 10, machines with X-axis travel from 1000 mm; and in the case of wire cutting EDM equipment, our models are the AV60, 80, 100 and 130, machines with X-axis travel from 800 mm.
Q. Each large machine version has different modular configurations depending on the paths of the X, Y and Z axes. There are, for example, 20 different possible configurations for the ONA IRIS7 machine. How does a company know whether to opt for one or another model or configuration within the same range of large machines? Is it just a question of workpiece size? Does ONA advise its customers on this?
A. The size of the part to be manufactured is what defines the main characteristics of the model to be used for machining the component: machine axis paths, work tank dimensions, minimum distance between work table and spindle, etc. The customer themselves, depending on the type of parts to be machined, can define the main characteristics of the machine they need and choose the configuration they require from among the many that we offer for each model. ONA provides the customer with further advice on the choice of additional accessories that can be included. This is the type of information we give our customers, since sometimes modifications need to be made in the electrode changers in order to adapt them to the type of electrodes or electrode clamping tools used by the customer. Occasionally, the machine also needs to be adapted to fit the customer’s floor space, meaning that some peripheral elements (filter, generator or external electrode changer) need to be repositioned in order to fit the whole unit into the available space. Finally, I would also point out that we are receiving more and more requests for advice on the advantages of using twin-heads in the case of die sinking EDM machines.
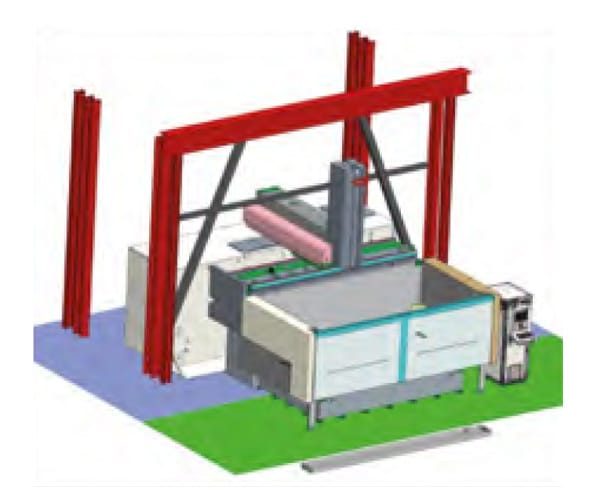
Feasibility study for the installation of an IRIS10 machine for a customer with limited floor space due to columns.
Q. For what kind of applications/parts and in which industries are ONA’s large die sinking and wire cutting machines typically used?
A. In the specific case of large die sinking EDM machines, the main customer sector is the manufacturer of plastic injection moulds for external vehicle parts, such as bumpers, or interior parts, such as dashboard instrument panels or doors. To a lesser extent, within the automotive industry, the manufacture of aluminium and zamak injection moulds is also important, both for structural parts of the vehicle chassis and for engine parts (crankcases, gearboxes, etc.).
Other important customer sectors include the manufacturing of power generation turbine components, as well as turbomachinery components used in gas extraction, compression and distribution.
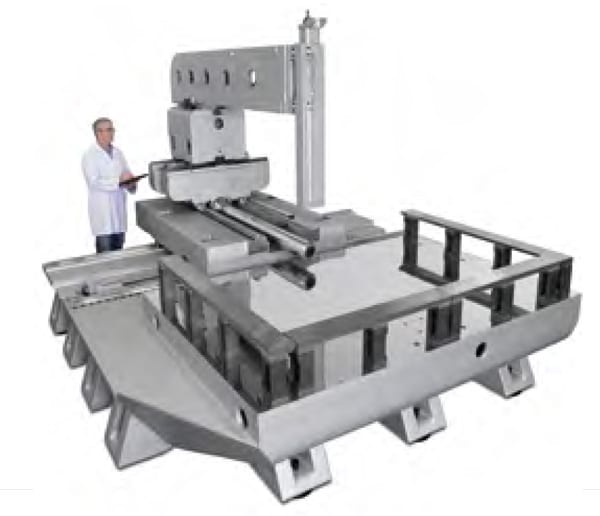
Q. The IRIS10 die sinking and AV130 wire cutting machines are the largest EDM machines on the market. What main features would you highlight for each of them in terms of business/customer needs?
A. The IRIS10 features a large Y-axis path of up to 1500 mm, which can be extended by ±250 mm if a 250 mm long horizontal extension rotary indexing table is incorporated into the head.
As for the AV130, I would highlight the combination of the Y-Z axes, which reach paths of 1300 x 800 mm. No other wire EDM machine on the market offers such an extensive combination of paths.
Q. The IRIS 10 die sinking machine can handle workpieces up to 25 tonnes, and the AV130 wire cutting model can process workpieces up to 10 tonnes. What applications are such large parts used for?
A. In the case of both the IRIS10 and AV130 machines, these parts are manufactured for large plastic injection moulds. Although the AV130 has a standard 10 ton maximum load capacity, there is the possibility to reinforce the machine’s structure and work table to increase this capacity to 25 tons.
Q. What advantages do these large EDM machines offer over more traditional machining techniques such as broaching and milling?
A. EIn the case of wire EDM machines, I would highlight three major advantages over broaching. Firstly, the investment cost itself, which is much lower than that of broaching machines. Secondly, the versatility offered by wire cutting machines over broaching machines. On a wire cutting machine, the profile of the workpiece to be cut can be easily changed, since the cutting tool is the wire, which is a standard consumable. However, on broaching machines, changing the profile of the workpiece requires a change of cutting tools (broaches). These tools are very expensive and have to be custom designed and manufactured for the final part to be machined. Finally, the low installation costs of a wire EDM machine compared to those of a large broaching or milling machine also need to be pointed out.
Q. Is ONA the world’s only supplier of large machines? What makes ONA’s machines special or different compared to those of your competitors?
A. Besides ONA, there are other manufacturers. But ONA is undoubtedly the supplier that offers the most extensive range of large EDM machines on the market, and also the one with the longest track record in the manufacture of this type of machine.
As early as the mid-1980s, ONA was already a forerunner in the manufacture of large die sinking EDM machines with a gantry type structure. We have also been pioneers in wire cutting EDM technology. One example of this was the presentation of the largest wire EDM machine ever launched at the EMO trade fair in Paris in 1999: the ONA Arion K1000, with X-Y-Z paths of 1500 x 1000 x 600 mm. To some extent, this was the year that marked the kick-off of the industrialisation of large wire cutting EDM machines, and today it is standard practice for most manufacturers to have wire EDM machines with a 600 mm Z-travel in their portfolio. Something that 23 years ago was only marketed by ONA.
Q. ONA began by marketing standard machines, then it had to adapt to market needs and opted for machines with a double head gantry structure, and finally, 25 years ago, twin head machines were first introduced, which been constantly improved ever since. How do you remember this progression? Did ONA’s specialisation in large machines and specific solutions come naturally or was it (and is it) a strategic move by the company?
A. Specialisation has come at the same time, both naturally and as a strategic move by the company. On the one hand, it has been the customers themselves who have asked us to develop ever larger and more complex machines. On the other hand, ONA is also deeply committed to implementing this type of solution because our company structure allows us to be more versatile and competitive compared to most of our competitors in this area.
As for our company’s evolution, I would say it was very fast, just as the current development of our technology is. Within a few years of launching the first gantry type EDM machine, we had already developed a complete range with several models of different sizes covering a range of electrode load capacities from 500 kg to 3000 kg in weight, including models with twin heads. This whole process took place from the mid-1980s to the mid-1990s. This is when a major change in the manufacture of plastic injection moulds occurred, with the widespread implementation of high-speed milling. The use of large electrodes that previously performed most of the mould machining was discontinued, and instead smaller electrodes were used for machining the grooves and cavities that were difficult to machine by milling. This change in trend led ONA to rethink the mechanical structure of the large die sinking machines, as the machines no longer needed to have a heavy gantry structure. Though this structure was suitable for working with heavy electrodes, it was not the best solution for optimal positioning accuracy. In the mid-1990s, the development of the new generation of large die sinking machines with a lighter, more precise RAM-type structure began. It is this type of structure that we still use today.
Q. What is the best thing about being a company specialising in large machines and dedicated EDM solutions?
A. It means a closer relationship with the customer, which in many cases increases the level of customer loyalty compared to those customers who buy standard machines.
P. What is the most difficult thing?
A. Special solutions require a high level of communication with the customer and cultural differences, which sometimes exist between companies in different countries or continents, can lead to greater complications than when selling standard machines.
Q. As ONA´s Project Director, what would you say is the most singular project (in terms of difference, complexity, relevance) that you have had to oversee over the years?
A. A: If I had to choose one, I would say Concours Technologies, as I consider it to be the most advanced large machine project in terms of automation and customisation. This was a TQX10 twin head machine tailored to the customer’s requirements, incorporating two electrode changing robots and fully integrated with the customer’s own in-house production management software.
Q. How do you envision ONA EDM in 25 years’ time, when, if all goes well, they will be a century old?
A. I imagine we will still be the stay the same as we are today: a company focused on improving customer satisfaction and strengthening customer relationships. If we look at who our current customers are, we can see that many of them were already customers decades ago, so I hope that in 25 years’ time they will still be placing their trust in us, as well as being able to earn the trust of those new customers we have yet to get to know our company over the coming years.