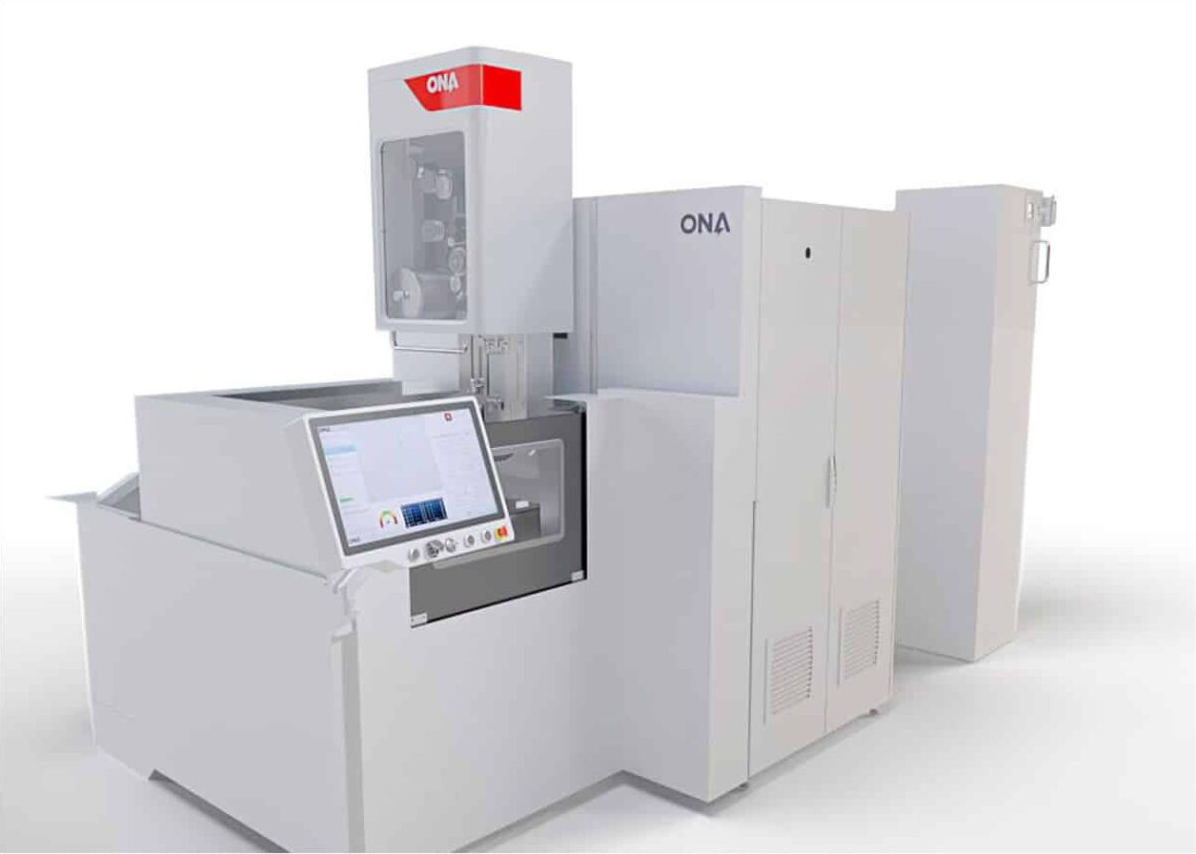
EDM for the machining of the largest turbine disc firtrees.
EDM for the machining of the largest turbine disc firtrees.
/ ONA’s WEDM technology has proven to be a match for conventional methods such as broaching and milling in terms of quality and precision, extending its capabilities to handle larger parts and providing manufacturers with additional versatility.
Being a pioneer in EDM research, especially for the aerospace industry, has been one of ONA’s main goals. Addressing the challenge of developing EDM technology adapted to specific processes has allowed us to position EDM as a competitive and high-quality machining method, even in comparison with more established techniques in the sector, such as milling and broaching.
ONA has also taken another step forward to offer a more efficient response to the manufacture of aviation turbine fir trees, which require high standards of quality and precision. With this new development, ONA has been able to adapt its EDM technology to produce larger parts, while maintaining high standards of quality and competitiveness in machining. This new wire EDM solution extends manufacturing possibilities, allowing the creation of larger components without compromising on precision and process efficiency.
Manufacture of larger parts
ONA’s new EDM solution can handle larger parts with greater ease. Based on the solid structure of the AV35 NEXT, this upgraded version offers an x-travel of 300 mm, a y-travel of 400 mm and a z-travel of 250 mm. In addition, it features a 45 kg coil for extensive autonomy and side access to the tank for easy maintenance.
Maximum adaptability to customer needs
The adaptability of the new model is another highlight. Unlike other EDM machines on the market, ONA’s new wire EDM machine stands out for its ability to adapt to a variety of applications. It is not simply a machine designed for a specific task, but can be configured with different accessories and modules according to the customer’s needs.
These are just a few examples of the manufacturing possibilities of the new model:
- Maximum weight: up to 250 kg
- Diameter: between 150 and 615 mm
- Maximum weight: up to 250 kg
- Maximum diameter: 545 mm
- Maximum height: 250 mm
- Surface finish: Ra<0.5um achieved with a maximum of 4 cuts.
Accessory components that can be added to the new model include:
- Sensor to ensure accurate part positioning,
- Script programming tools for the creation of intelligent measurement programs.
- 2-axis rotary table with pneumatic chuck for automatic and repeatable part clamping.
- ONA Smart Connect platform provides full part traceability and comprehensive process analysis, enabling monitoring of machining, statistics and failure prevention.
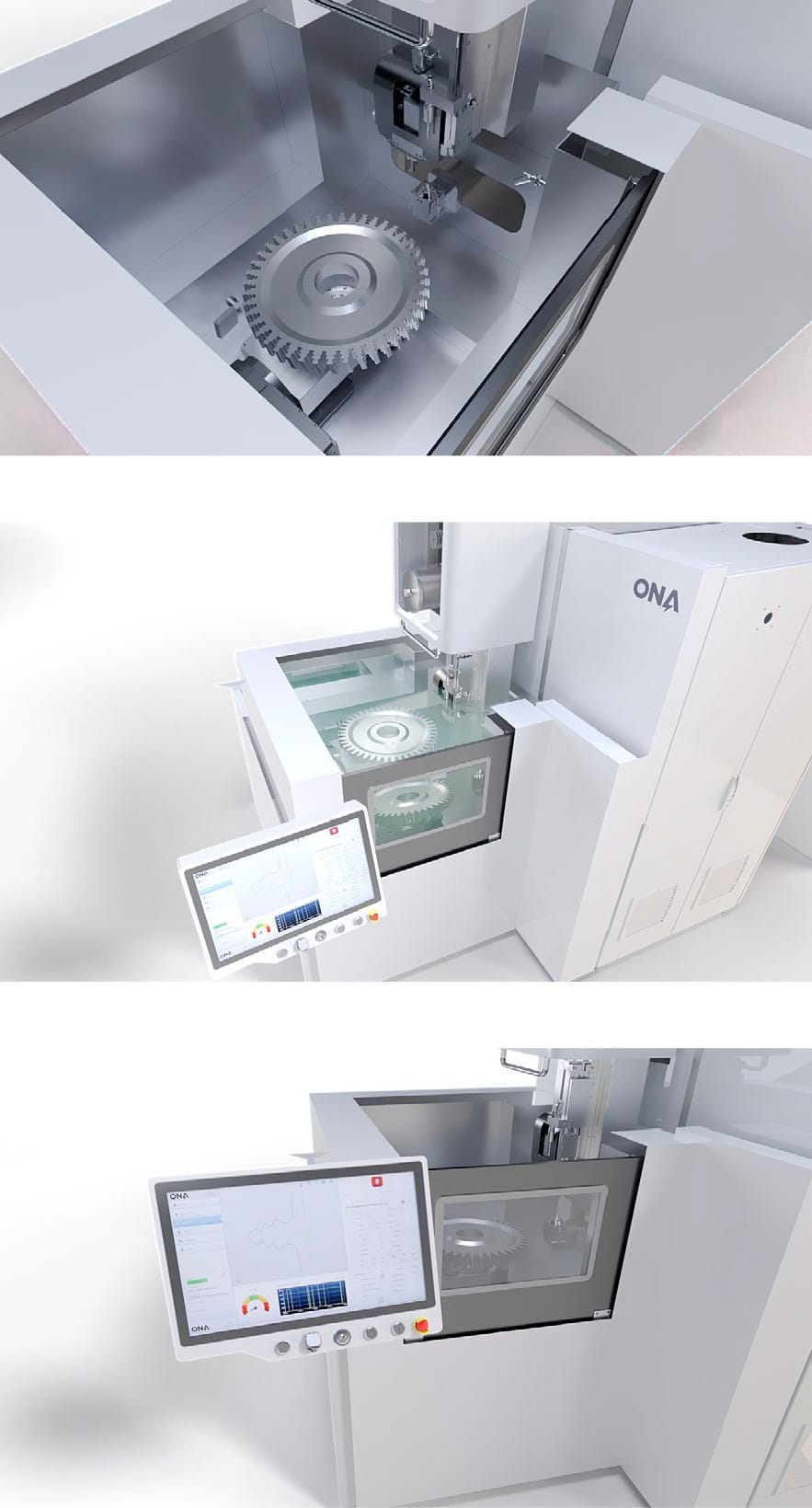
Technology on a par with broaching and milling
Manufacturing gas turbine discs involves significant challenges: these critical rotating components must withstand extreme temperature and pressure conditions, while maintaining high strength and being lightweight. Traditionally, machining has relied on chip removal techniques such as broaching, grinding and milling, with broaching being the most commonly used method.
However, EDM has emerged as an increasingly important and viable alternative. Thanks to the development of new generators, EDM has evolved into a competitive process for the manufacture of aircraft components, including turbine discs. These advances have led to increased power and productivity, together with improved surface and geometrical quality of parts, which are crucial aspects in the aeronautical industry. ONA’s WEDM technology, represented by its AV35 NEXT machine and now also this new improved version, has proven to be on a par with conventional methods such as broaching and milling in terms of quality and precision. The new development has not only led to advances in terms of quality and productivity, it has also extended its capabilities to handle larger workpieces. This improvement is of fundamental importance, especially in the manufacture of critical components such as gas turbine discs, which can be considerably large in size. This ability to work with larger parts gives manufacturers additional versatility and the possibility of tackling a wider range of projects without compromising the quality or efficiency of the manufacturing process.
EDM for the machining of the largest turbine disc firtrees.
ONA’s WEDM technology has proven to be a match for conventional methods such as broaching and milling in terms of quality and precision
Dubral optimises the precision and quality of its cutting with ONA AV35 model
The acquisition of the ONA AV35 model has allowed the company to improve the precision in its cutting, increasing efficiency
Sermec acquires the ONA AV35 machine to strengthen its EDM machining capacity
This fleet currently includes 4 wire EDM machines (AF25, AF35, AV25 and AV35), as well as a DR2 model erosion drilling machine.
ONA EDM technology optimises the performance of the MCM production process
The acquisition of ONA’s AV25, AV35 and AV60 models has meant an increase in profitability and quality for MCM and a high level of satisfaction.
Sabacaucho to machine large moulds for elastomeric parts with the ONA IRIS8 B1L+ machine
Sabacaucho’s requirement for a machine with a high capacity for machining and repairing larger moulds led the company to contact ONA.
Tecnijusta expands its capacity to manufacture larger moulds with the ONA Iris 6 machine
Tecnijusta acquires the ONA Iris 6 model to strengthen its capabilities and improve efficiency in the EDM process.