Advantages of incorporating wire-cut EDM for the machining of turbine disk firtree profiles for the aeronautics sector
\ Advantages of wire-cut EDM for the machining of turbine disk firtree profiles
One of its great virtues is that it is a standard machine. It has a basic structure to which modules/accessories can be added depending on the type of component to be manufactured. This allows for fully automated machining. Just replace or adapt some of these elements to manufacture different types of parts. The AV35 is one of ONA’s most ambitious projects in recent years: It represents our technological development of WEDM technology applied to the manufacture of highly demanding parts.
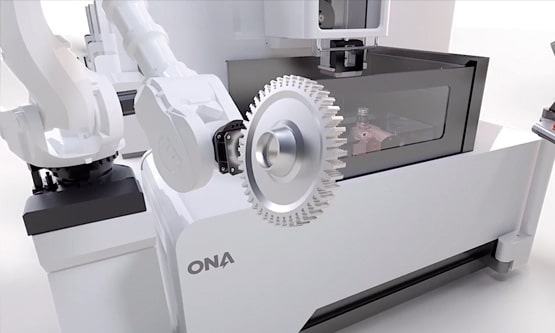
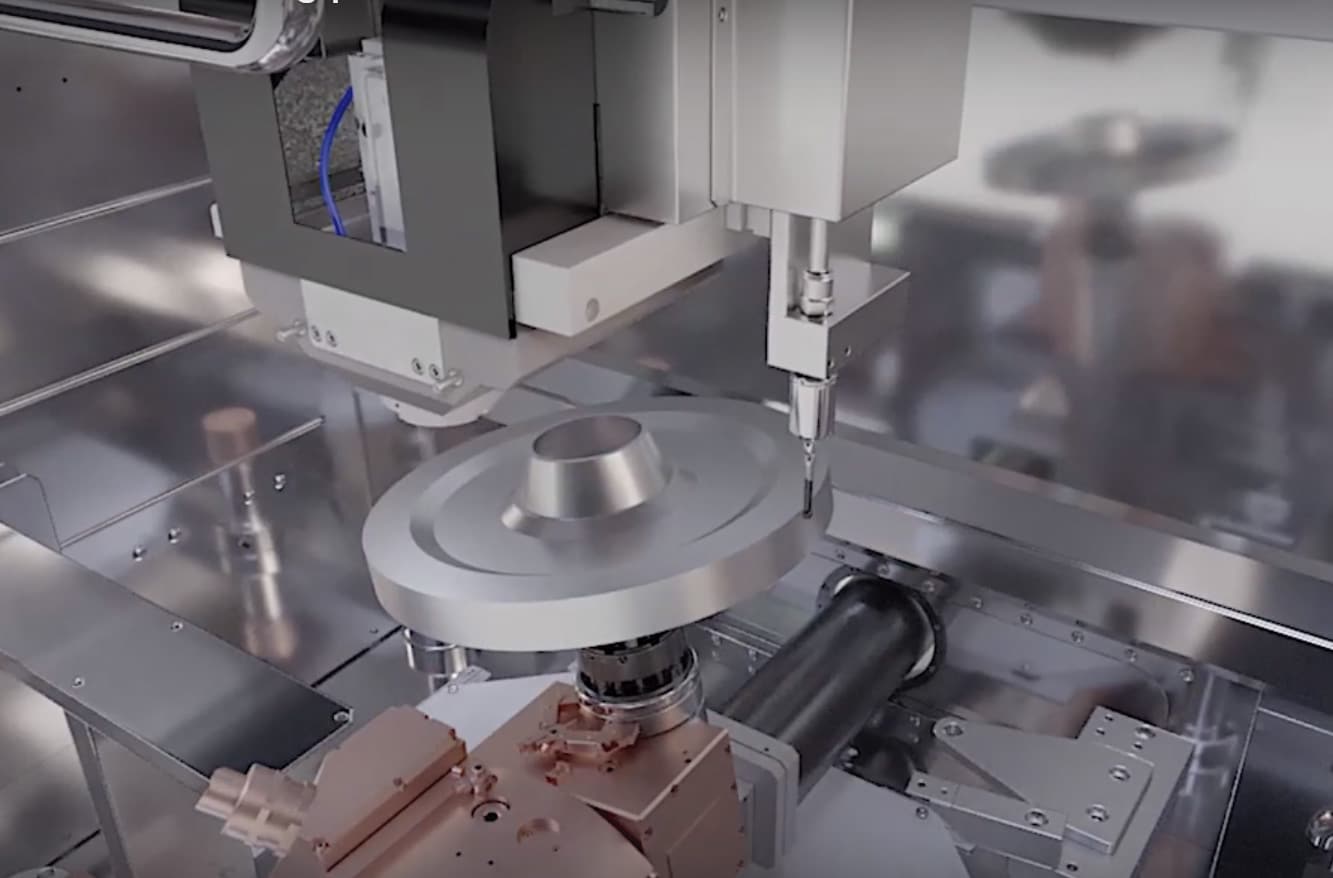
Touch probe
To ensure the correct positioning of the part.
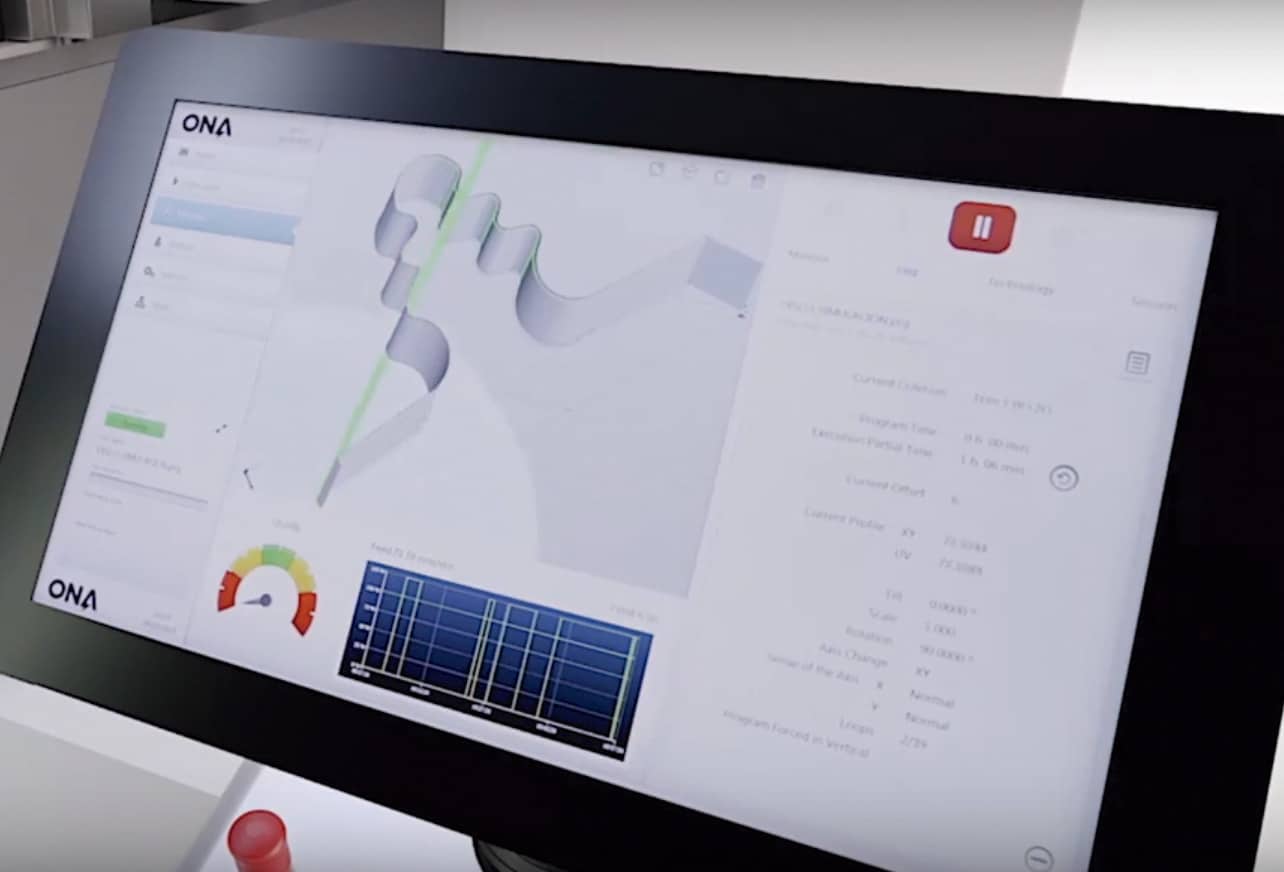
Script programming
Tool for the creation of smart ‘in-process’ measurement programs.
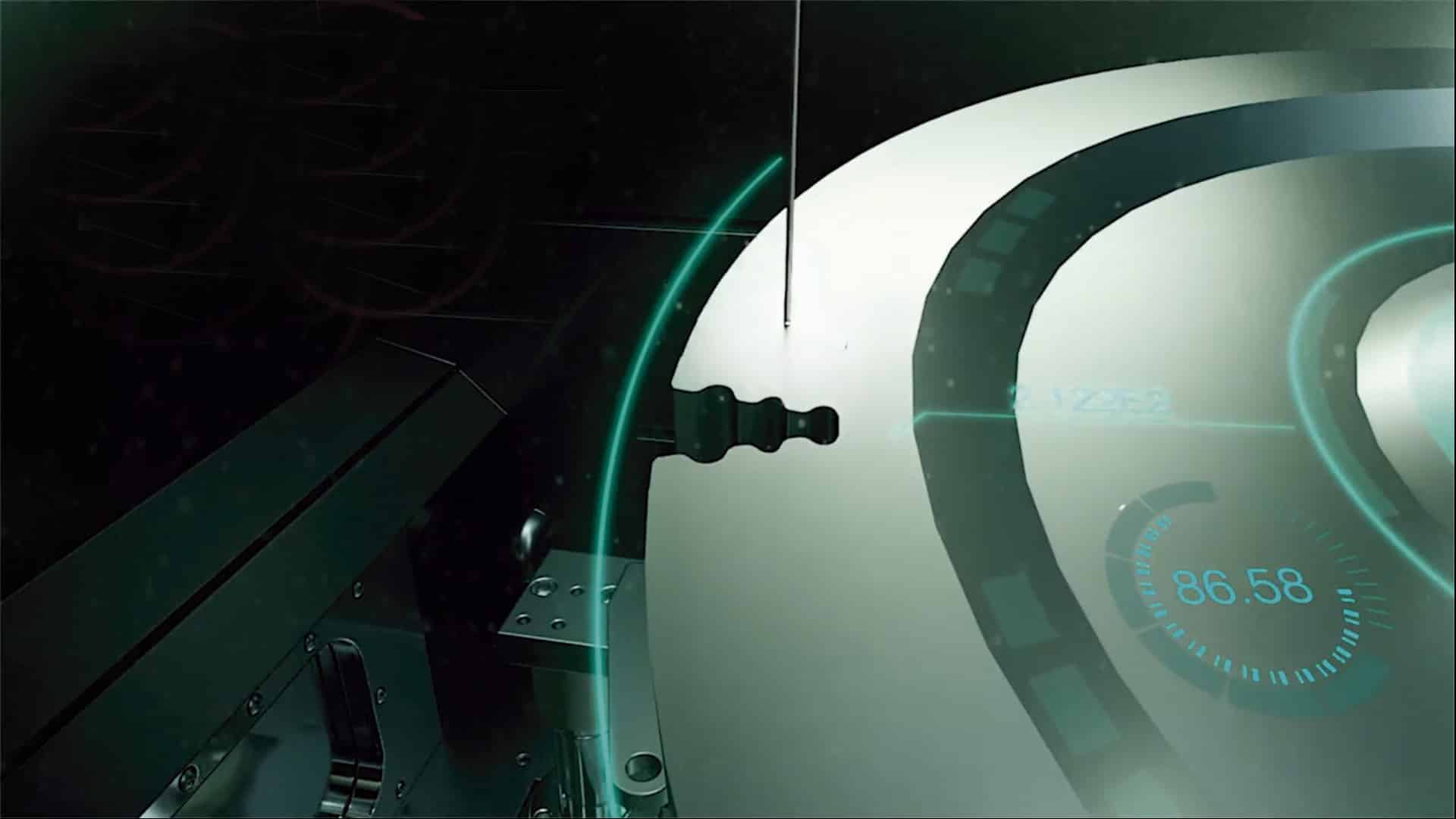
2-axis rotary table with pneumatic chuck
Automatic and repetitive clamping of the part. It enables the erosion of the part in a single bundle.
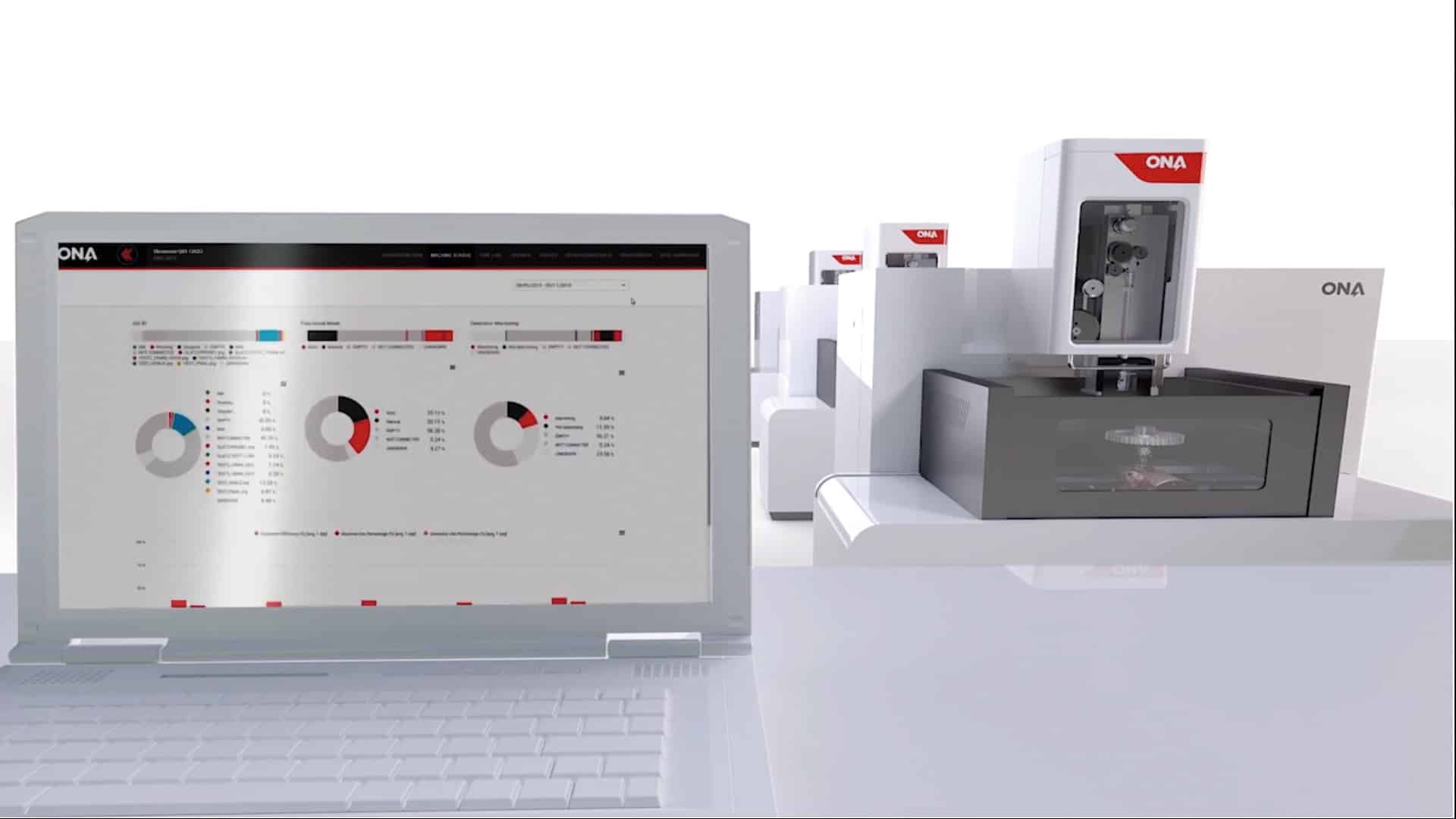
Full part traceability and process analysis thanks to the ONA Smart Connect platform
Option to monitor the machining of each section of the part, perform statistics, prevent errors, foresee maintenance tasks, trace the parts, etc.
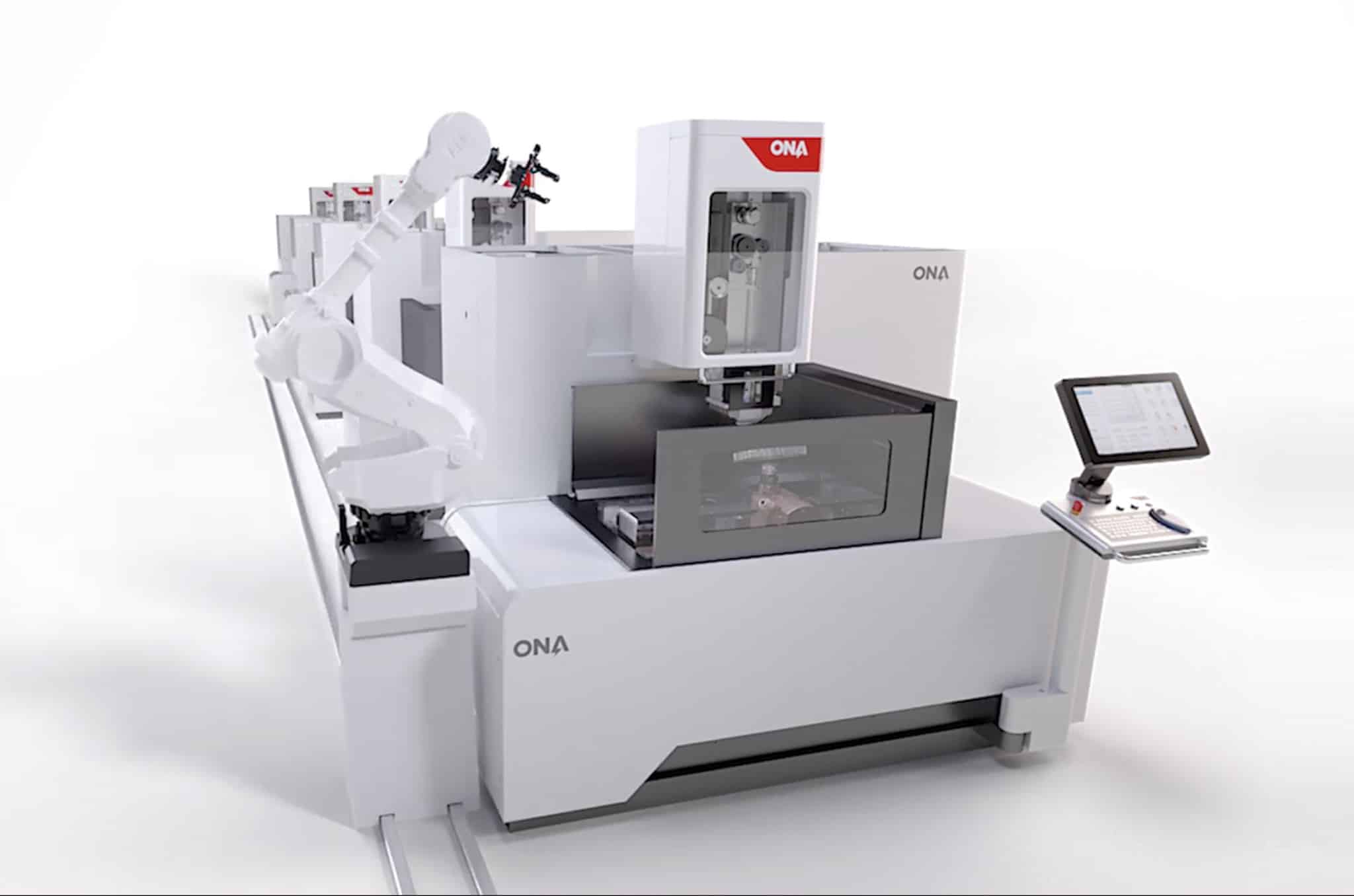
Automation of the whole process
Last phase: A robot has been added to keep the machine working day and night with the same accuracy.
To be at the forefront of research in electrical discharge machining for the aeronautics industry as well.
One of ONA’s greatest challenges has been to develop EDM technology adapted to the process in order to convert electrical discharge machining into a competitive and high-quality machining process, even when compared to some of the most common processes in the industry, such as milling or broaching.
An example of the latter is the cutting of fir-tree roots for aviation turbine discs, mainly manufactured by broaching.
A successful project to highlight is the work carried out in collaboration with a company in the aeronautics industry, project in which we manufactured fir-tree roots for aviation turbines on the ONA AV35 wire-cutting EDM machine (WEDM).
This is, without a doubt, one of the most important and ambitious projects ONA has partaken in recent years. On the one hand, our organization had to undergo a cultural change, since different departments had to work closely on the development of the machine. On the other hand, thanks to our hard work and the technology developed, the application was successful and the manufacturing process of highly demanding parts was validated.
There are currently few alternatives on the market to the AV35. What distinguishes the ONA AV35 from other EDM machines for the manufacture of fir-tree roots for turbine discs, is that the ONA AV35 is a standard machine to which accessories/modules can be added, which makes it able to adapt to the manufacture of other components. In other words, this equipment is not manufactured exclusively for one purpose.
Developing the machine required many hours of research by our team, but it was worth it. ‘The most complicated part was coordinating with different departments as well as with the client. The machine was designed according to the specific needs of the clients. We had to use state-of-the-art software tools to comply with the traceability requirements’, describes one of our technicians.
The AV35 offers important advantages to companies, such as a lower initial investment in machinery, thanks to this adaptability, and more autonomy. The entire machining process is automated and rigorously controlled so that the part meets the requirements set out: Data and parameters are continuously provided to monitor whether progress is being made as programmed and, in the event of any error (a change in water temperature, etc.), a warning signal is emitted.
Technology at the level of broaching and milling
Discs are critical rotating parts in a gas turbine: They reach up to 60,000 revolutions per minute and must be able to withstand extreme temperatures and pressure fluctuations, while being lightweight and safe. The quality of the material used (usually nickel-based superalloys) and the machining process (high geometrical and surface quality requirements) are therefore essential.
The most commonly used machining techniques to manufacture turbine disc fir-tree roots have traditionally been physical machining processes: Broaching, grinding and milling. Broaching being, perhaps, the best known and most used process.
With regard to electrical discharge machining, the development of new generators has been the main drive that has made EDM a viable and competitive manufacturing process for the manufacture of components in the aeronautics industry. The main advantages of developing new EDM generators are: The capacity to provide a higher power output, thus increasing productivity; and the adaptation of the technology and machining strategy to reduce the heat affected zone as well as the white layer, which are indispensable, especially in the aeronautics industry.
These and other advances have gradually brought our technology up to the level of broaching and milling in terms of quality of the final product. And today it can be said that, in addition to achieving the strict tolerances required for aircraft parts, ONA’s WEDM process also offers turbine manufacturers greater flexibility in terms of deadlines and references: It allows them to adapt faster than conventional machining processes would allow them to.
ONA’s AV35 machine minds all the details: From the part positioning compensation, to the optimization of technology and total connectivity for a perfect traceability of the whole process.