\ Additive Technology – Laser beam powder bed fusion
In recent years, additive manufacturing has experienced a spectacular increase due to the important advantages it offers, since it produces highly complex parts in less time and at a very competitive cost. Meet our additive manufacturing companies Addilan and Samylabs and transform your industrial processes.
The democratisation of metal printing is here.
In just a few hours create the spare parts you urgently need, but also decorative figures, moulds, stamps, prototypes… Reduce the number of manufacturing components to just ONE. The applications of ONA SAMYLABS are infinite.
There are many options for 3D metal printing… What makes ONA SAMYLABS the best option for your projects?
The democratisation of metal printing is here.
In just a few hours create the spare parts you urgently need, but also decorative figures, moulds, stamps, prototypes… Reduce the number of manufacturing components to just ONE. The applications of ONA SAMYLABS are infinite.
There are many options for 3D metal printing… What makes ONA SAMYLABS the best option for your projects?
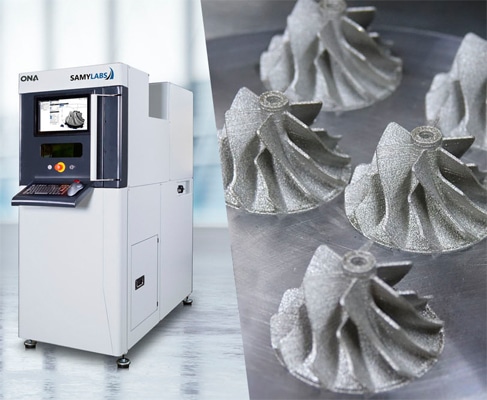

Why choose the
ONA SAMYLABS printer?
There are many options for 3D metal printing… What makes ONA SAMYLABS the best option for your projects?
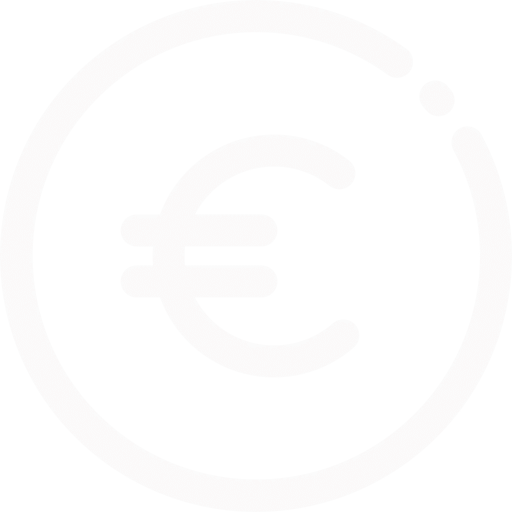
High-quality at an affordable price
ONA SAMYLABS has an unbeatable price-quality ratio and is made in stainless steel; perfect for the workshop, office or lab, and in addition it operates on domestic power supply current.
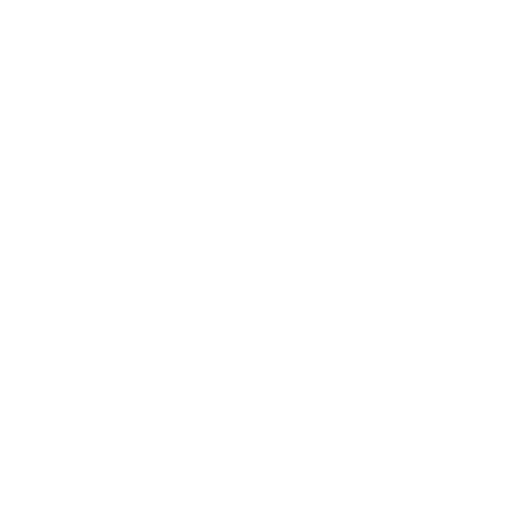
The all-in-one option
Our own cutting-edge technology, perfect size, ease of use, without future costs and with all the accessories you may need.
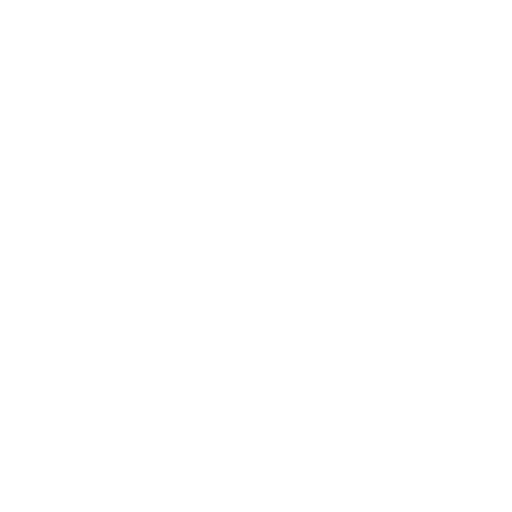
Ergonomic and easily cleaned
Its 730 x 1550 x 1850 size enables it to pass through conventional doors, it meets the most demanding safety requirements and is easy to clean.
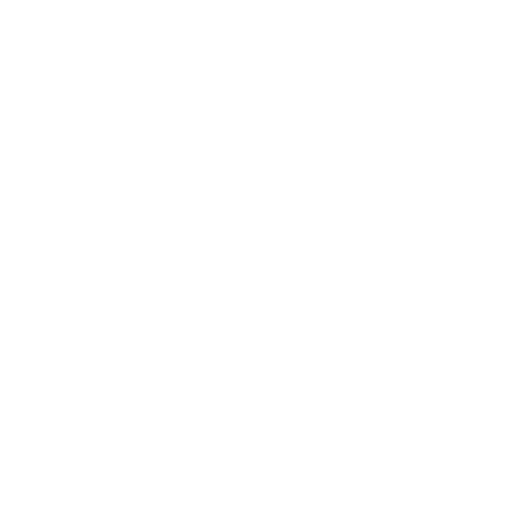
Single-payment own software
Our own slicing and control software, fast printing, free licence and single payment modality, so that you can be totally independent.
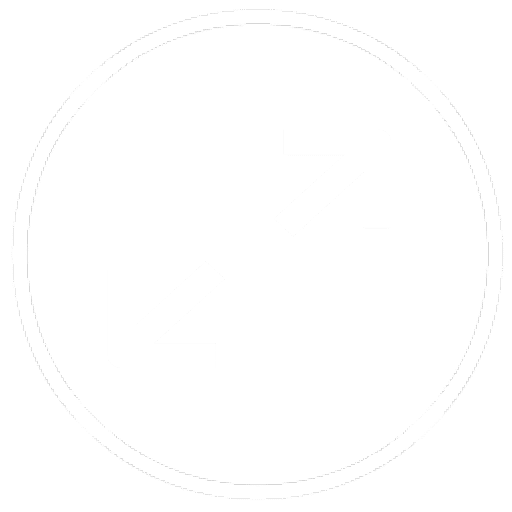
A deposit 160 mm in diameter x 200 mm in height
A deposit 200 mm in diameter x 250 mm in height
Its large filter enables a larger printing volume and high repositioning speed.
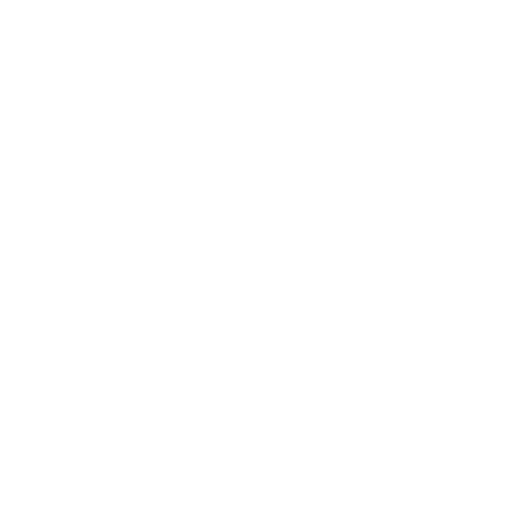
Its own high-power laser control system: 300 W.
High-technology with our own electrical, electronic and mechanical design.
Find out more about these machines
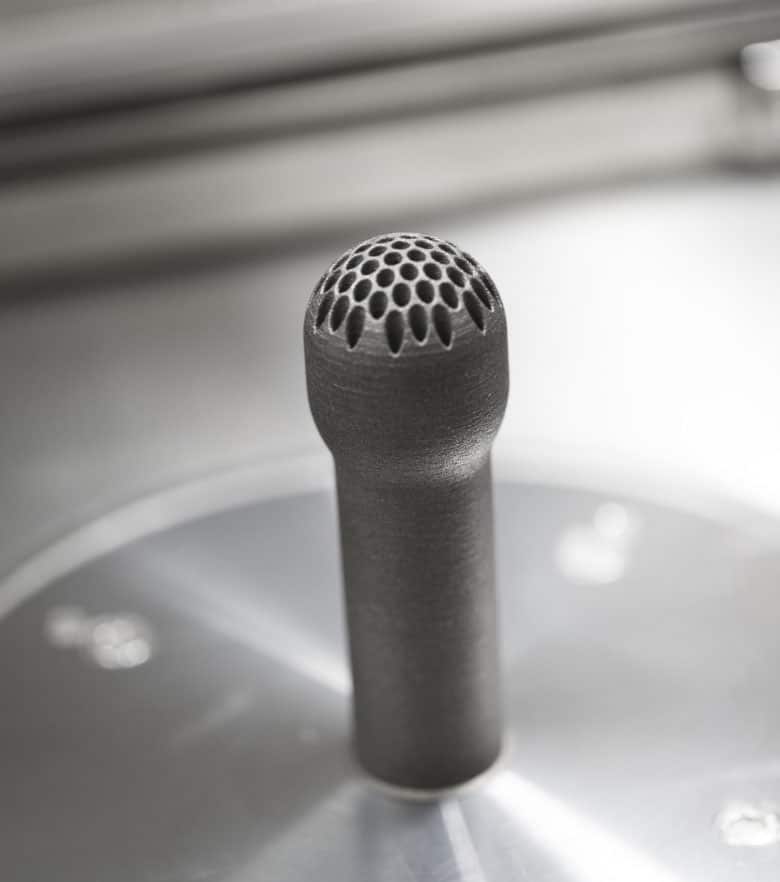
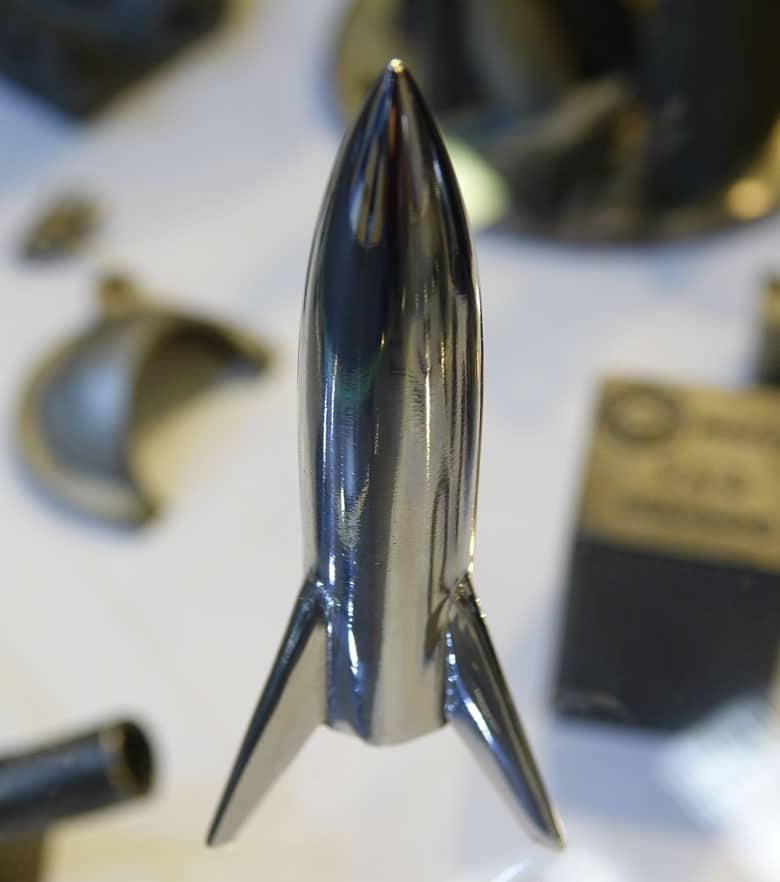
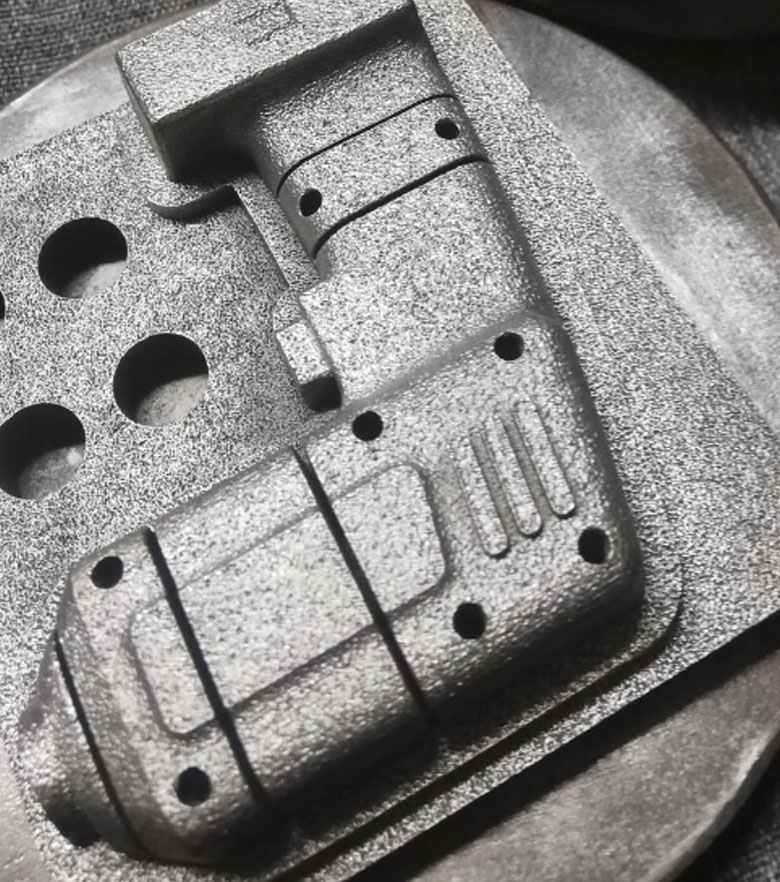
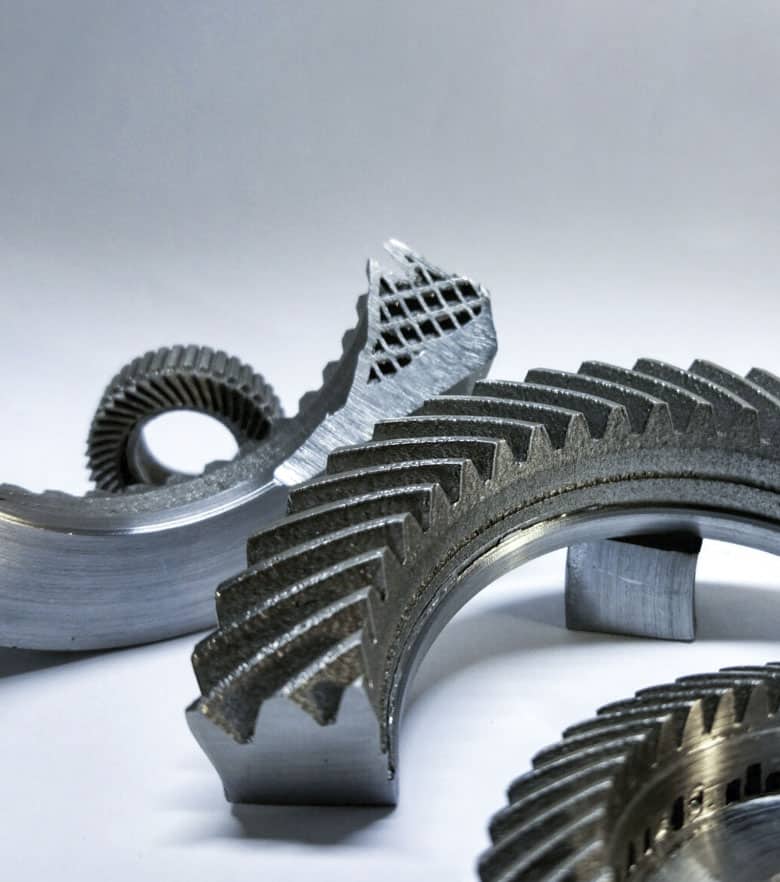
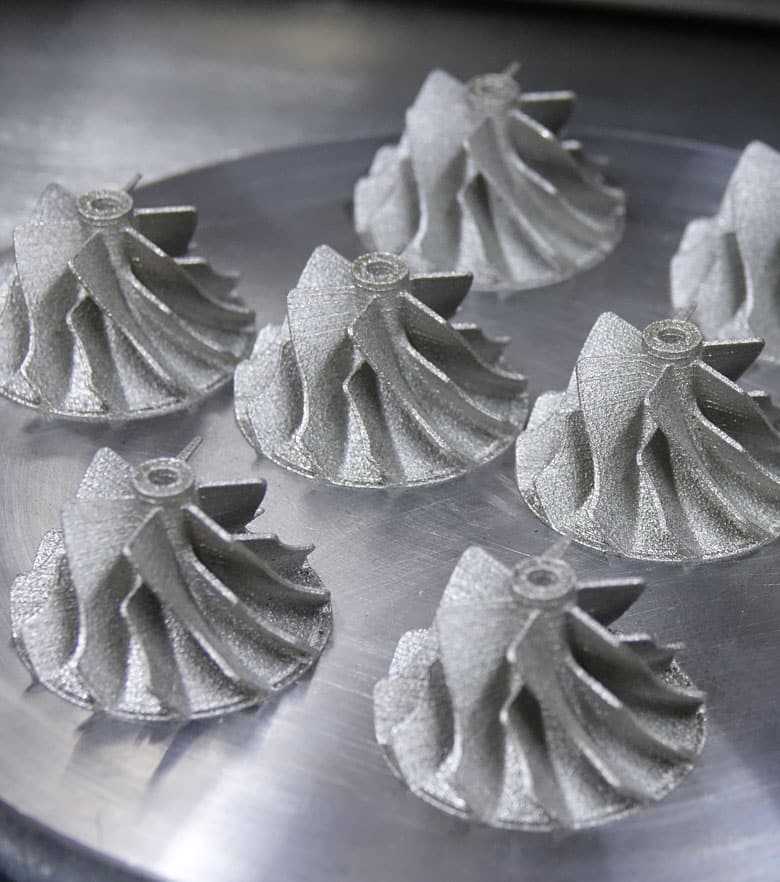
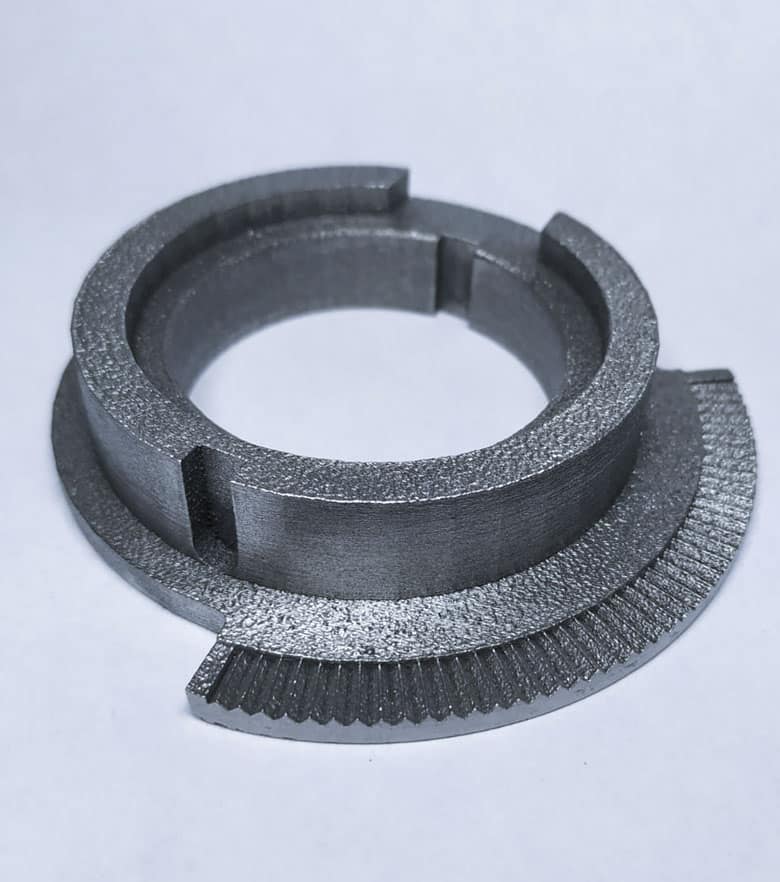
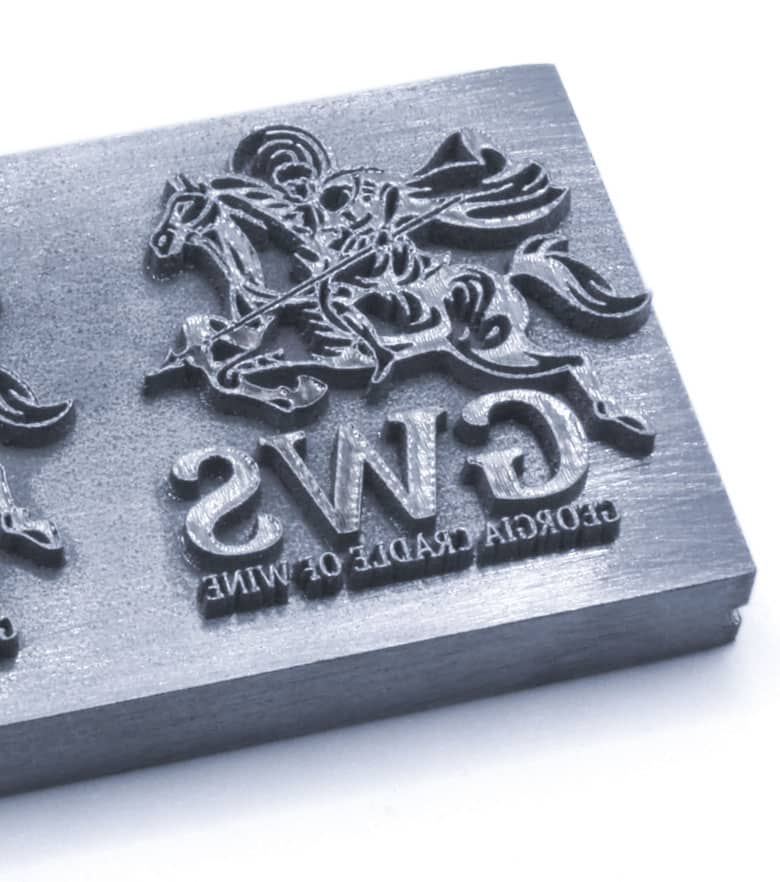
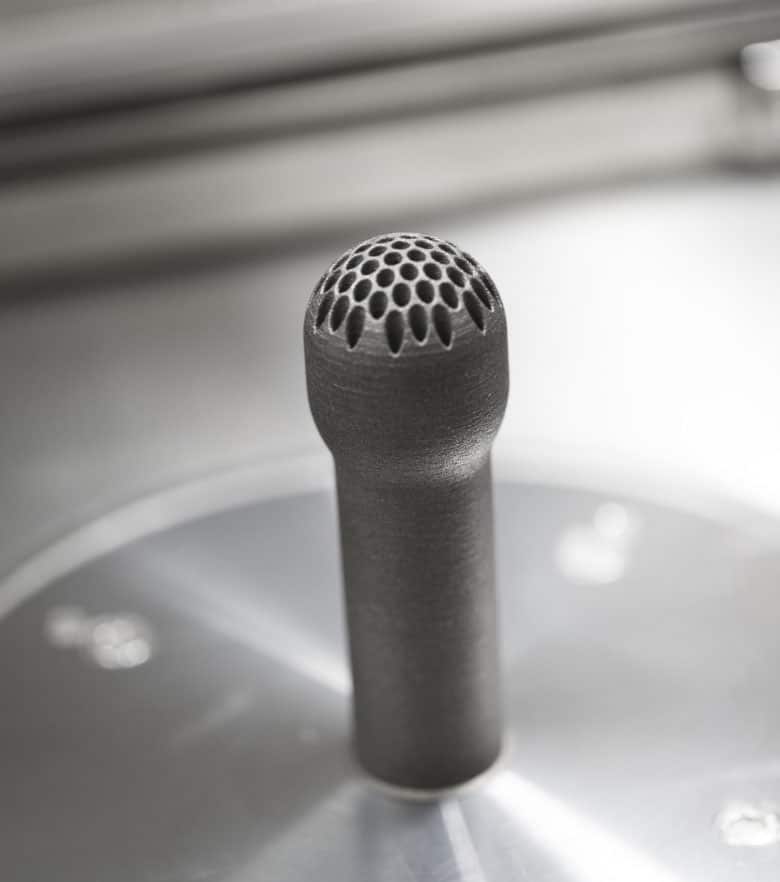
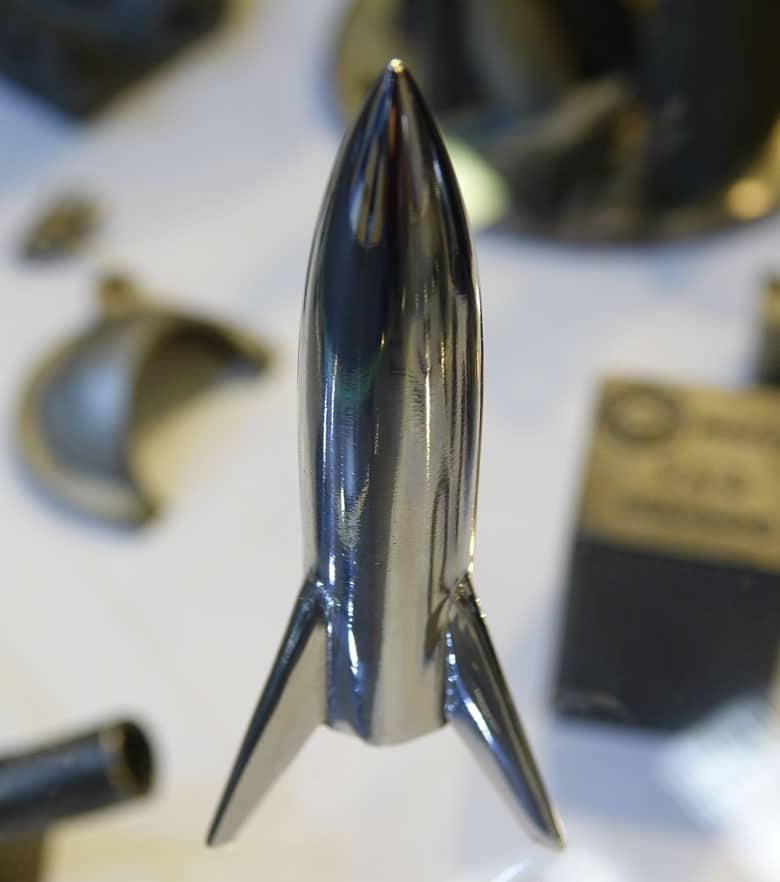
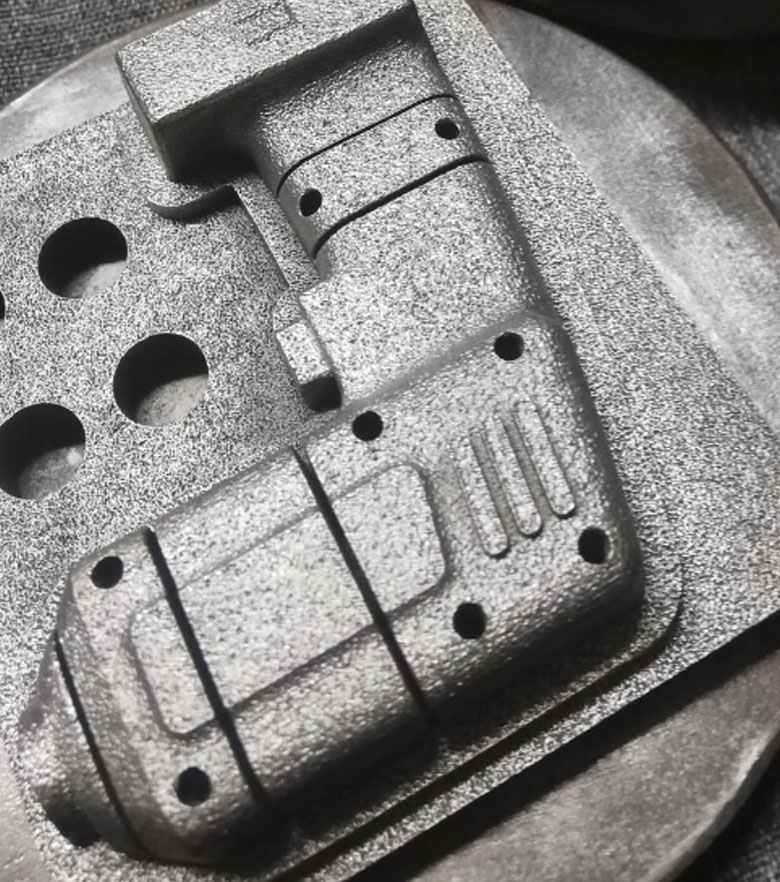
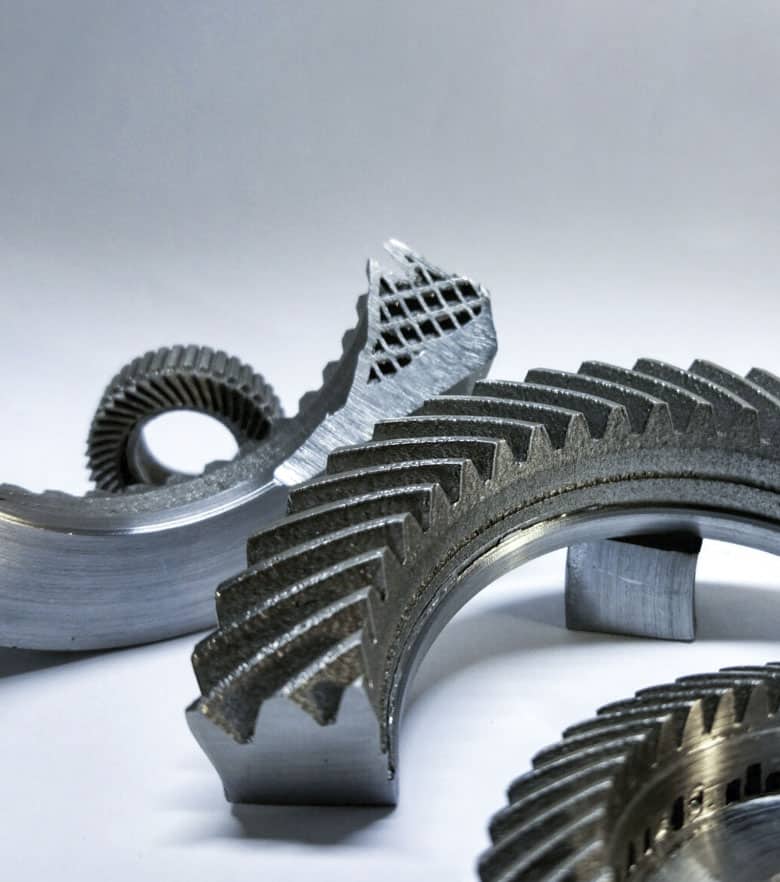
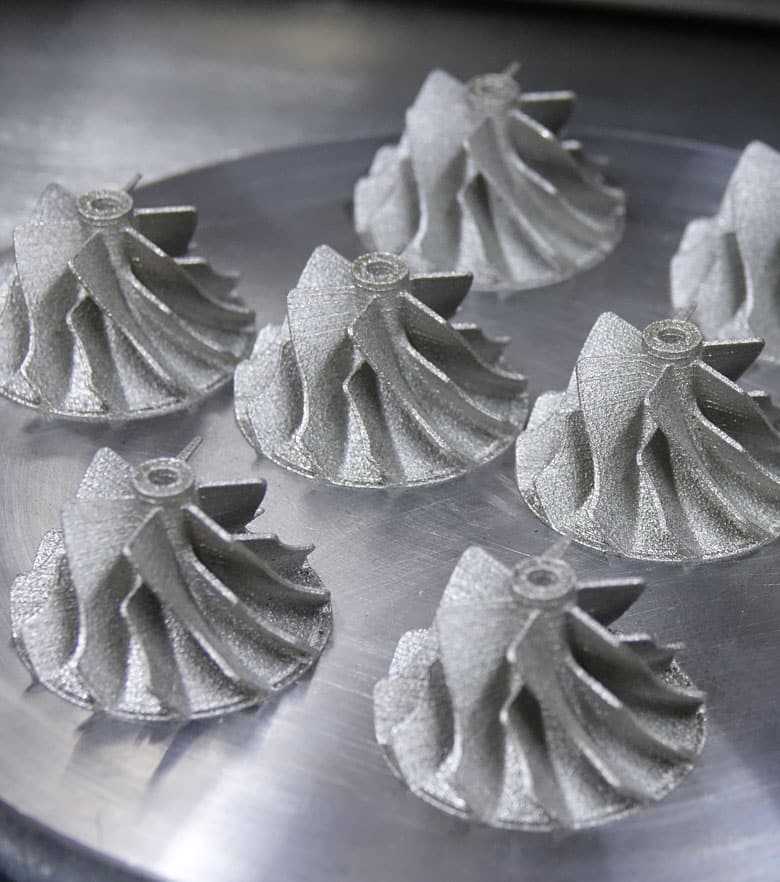
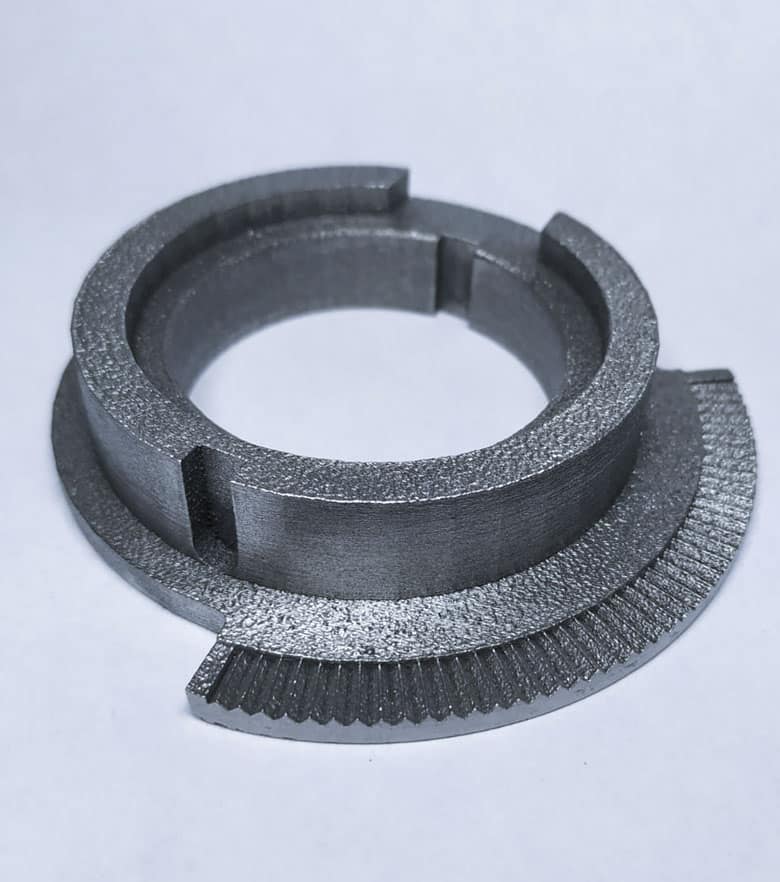
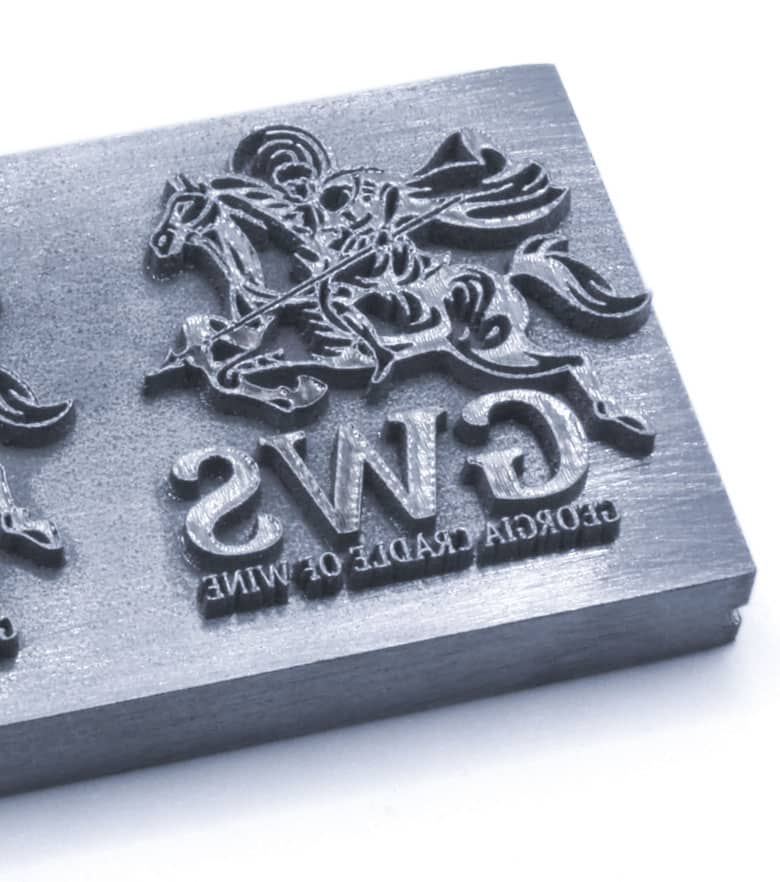
Laser beam powder bed fusion technology
The technology of 3D printing in metal by laser allows to obtain final parts with excellent mechanical qualities, which in many cases are impossible to manufacture by other means. Powder bed melting is the leading technology for the manufacture of precision metal objects with complex geometries. It allows to reproduce practically any geometric shape in different metallic materials such as Stainless Steel, Tool Steel, Inconel, Cobalt-Chrome and many other alloys.
High density values are achieved, above other additive manufacturing techniques in metal. This technology is very useful for manufacturing final parts with very complex geometries and structures with thin walls and/or hollows or hidden channels.
Powder Bed Melting
Final parts with excellent mechanical qualities and that in many cases are impossible to manufacture by other means.
It allows to generate within the parts, support structures and internal filling that provide an important resistance to pressure, torsion, and traction tests, with a considerable reduction in weight. These types of structures are known as “bird bone”.
The technique allows to play with the density of the material avoiding the internal pores that occur, for example, in the injection processes.
Printing by means of a high-power laser beam (>200 W) on a bed of metal powder, using a galvo head that moves two mirrors at high speed.
The layer ranges from 20 to 100 microns.
Long machine life which has much less mechanical wear.
Manufacture of high precision parts in stainless steel (A316L), tool steel (C300) and inconel (IN718) , Aluminum (AlSi10Mg) and Titanium (Ti6Al4V).
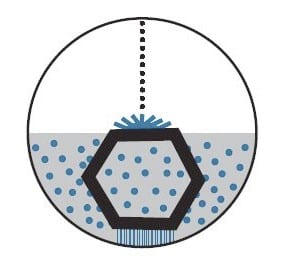
ADDITIVE MANUFACTURING
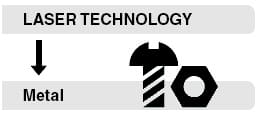
The characterization of Aluminum AlSi10Mg has been carried out by the IMH center within the ICME ELKARTEK 2021 program (file number KK 2021 00022) obtaining and testing horizontal and vertical specimens according to the UNE EN 10002 1 standard for the characterization of mechanical properties both in the X Y plane as in the Z axis of the machine.
Powder Bed Melting
Final parts with excellent mechanical qualities and that in many cases are impossible to manufacture by other means.
It allows to generate within the parts, support structures and internal filling that provide an important resistance to pressure, torsion, and traction tests, with a considerable reduction in weight. These types of structures are known as “bird bone”.
The technique allows to play with the density of the material avoiding the internal pores that occur, for example, in the injection processes.
Printing by means of a high-power laser beam (>200 W) on a bed of metal powder, using a galvo head that moves two mirrors at high speed.
The layer ranges from 20 to 100 microns.
Long machine life which has much less mechanical wear.
Manufacture of high precision parts in stainless steel (A316L), tool steel (C300) and inconel (IN718) , Aluminum (AlSi10Mg) and Titanium (Ti6Al4V).
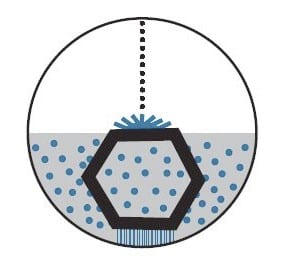
ADDITIVE MANUFACTURING
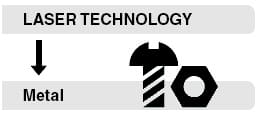
The characterization of Aluminum AlSi10Mg has been carried out by the IMH center within the ICME ELKARTEK 2021 program (file number KK 2021 00022) obtaining and testing horizontal and vertical specimens according to the UNE EN 10002 1 standard for the characterization of mechanical properties both in the X Y plane as in the Z axis of the machine.
CASE STUDIES
Alba 300 machine, ONA commits to metal Additive Technology
Metal Additive Technology. At ONA we have one of the most competitive metal 3D printers in this market, the Alba 300 from Samylabs.
ADDILAN perfects additive manufacturing with infra-red technology
ADDILAN perfects its metal additive manufacturing process and includes infra-red technology to control the whole process in real time.
ONA MACHINES AROUND THE WORLD