Innovation and profitability: Double head EDM machines: Savings of 50% in the erosion time and up to 200% of productivity. Half the time for the same results.
\ Double head EDM machines: up to 200% of productivity
The possibility of including a second head in our larger machines, controlled by an independent CNC, makes the ONA models highly profitable solutions. Erosion time is reduced by up to 50% and there is an increase in productivity of up to 200%. Half the time for the same results.
Innovation and performance are combined in our double head machines. Two machines sharing the working tank, which means less space and a greater optimization of the work process. Enhanced profitability by manufacturing the same in half the time.
These models can work as two independent machines, by separating the tank with a moveable door, or remove it to make a single machine with a double head specifically designed for the manufacture of large pieces and different cavities. This separation of the tanks implies that both can work independently with different dielectric levels, different tool changers, different CNC controls. Provides lots of flexibility to work on the same mold at both ends simultaneously or turn the large machine into two independant machines sharing one machine base.
A significant competitive edge for our clients. They can cut the delivery time for their workpieces in half, and obtain great profitability, particularly with jobs requiring many hours of erosion.
Within the framework of constant innovation and continuous improvement, ONA’s R&D department works daily to include technological improvements in its double head models.
Constantly striving to adapt to the client’s needs, ONA has been manufacturing double head equipment with its current structure for 24 years. Six years prior to that, ONA had already produced machines with a double head gantry structure and was one of the first manufacturers to develop this technology. Years of proven experience perfecting the technology of its equipment to become world leaders in the manufacture of this type of machines.
In this past year, the double head models have incorporated the following improvements:
- Regarding the mechanics, the distance between heads can be modified to the client’s specifications.
- A vertical extension with double automatic changer. Two chucks are included (in the C axis and at the extension point). This helps optimise the use of the electrodes with end of extension and erode at a greater distance without colliding with the head.
- Both heads work in collaboration with an automatic interference management system. Both heads communicate with one another and control the common erosion areas, thus avoiding collision. One head checks the other before making a movement.
- Automatic adjustment of the dielectric level constantly maintained at head level. The machine knows the exact location of the head at all times and adjusts the dielectric level to said position. The electrode is always covered by the dielectric, thus preventing programming errors.
- It integrates a especially designed software for double head machines, thus helping to manage the work of the two machines.
- New automatic chuck for large electrodes. Heavy weight electrodes can be interchanged while maintaining the C axis.
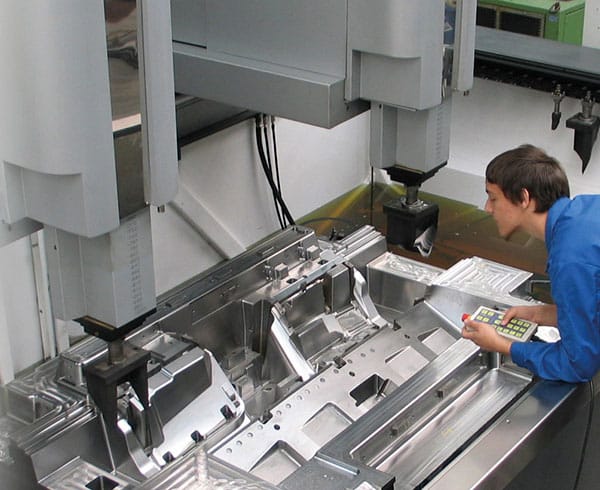