Custom EDM solution: Drilling Diffuser holes in turbine blades.
\ Custom EDM solution: Drilling Diffuser holes in turbine blades.
ONA’s business strategy in the aeronautical industry largely involves providing companies with customised, high added-value solutions. One example of this was the development of a custom application for an important manufacturer of high- quality components used in the aerospace and energy industries. Their need for such high-quality products was a key factor in their decision to opt for ONA.
The customer required a solution for drilling diffuser holes in turbine blades. These holes play an important role in ventilation and cooling. Poor ventilation and cooling increase turbine air inlet temperature and eventually reduce the component’s efficiency and durability. In a power generation turbine, less energy would be produced, and in a propulsion turbine (such as an aircraft turbine) more fuel would be consumed. Furthermore, high temperatures may also end up damaging the compressor blades themselves.
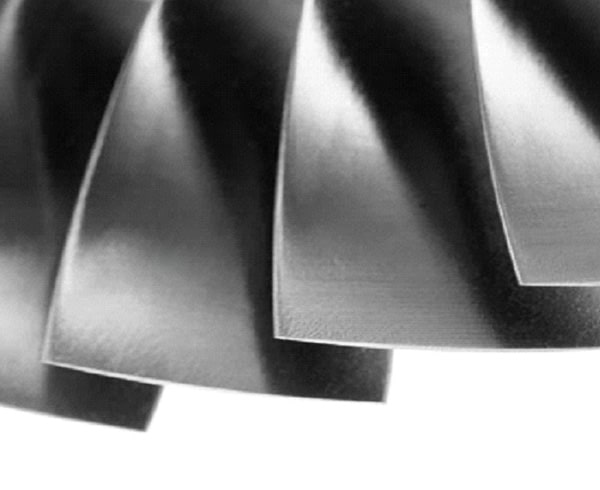
The holes in the blades are normally machined using our FAST HOLE (FH) machinery that uses specialised technology for faster machining speeds. However, the manufacturer’s high precision and quality requirements for drilling the holes (with different geometric shapes: conical, trapezoidal, etc.) could not be met by our FH equipment, so they asked ONA to provide a specific solution to this problem.
Our engineers’ proposal was to develop an application that would combine the capacities of two EDM technologies: FAST HOLE and die sink EDM. First, cylindrical holes are drilled into the workpiece by means of an FH machine and then, by using an ONA IRIS 6 machine (XYZ- axis paths: 1000 x 750 x 650 mm; with a 2-axis rotary table and copper electrode), other holes with the required geometric shapes are also drilled into the first holes. The axis of some of these holes may not be parallel to the axis of the first hole.
How we managed to do it
One difficulty in implementing this project was the global situation at the time. Finding ourselves in the middle of the Covid pandemic, face-to-face meetings between ONA’s team and the customer were impossible. This challenge was met thanks to the excellent collaboration between ONA’s different departments and our digital expertise, which allowed us to eventually send a telematic tender to the end customer.
Faced with this scenario, and for the customer to fully appreciate how the process was going to be carried out and the problem solved (the whole EDM diffuser process), a full simulation was performed using our CAD/CAM software. The stages involved in conducting this simulation were as follows:
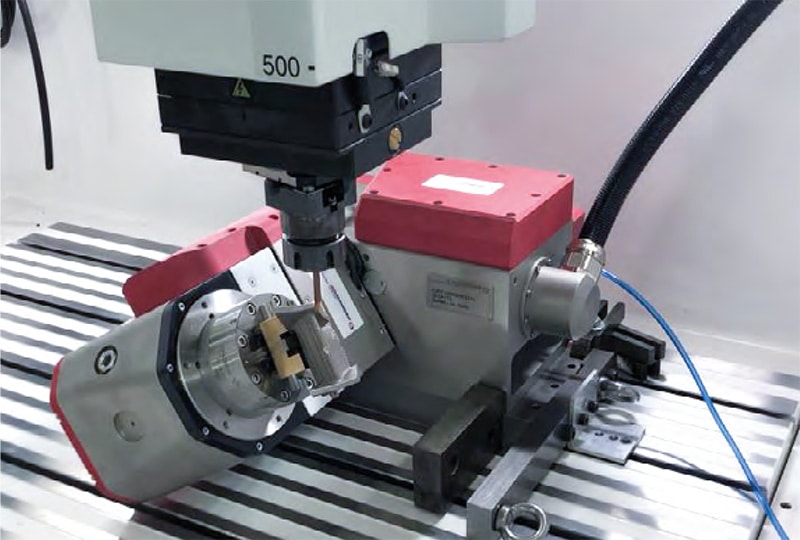
-
Feasibility and final quality assessment study.
First, a feasibility and final quality assessment study was carried out to check whether the test could be carried out using an ONA machine. This simulation was carried out in China on a machine in the subsidiary’s showroom.
-
Suitability of the ONA IRIS6 machine.
One of the conclusions of this preliminary feasibility study was the suitability of the ONA IRIS6 machine given the characteristics of the project: the size of the parts and need for a rotary table to drill all holes and be able to rotate the workpiece. In the case of the electrode, we decided to use copper to obtain a higher quality finish.
-
Tender on video.
Given the situation of the pandemic, the limitations imposed on and interest shown by the customer in wanting to go ahead with the project, ONA submitted the tender on video, expressing our total faith in the quality of the final workpiece.
-
View and link with CAD-CAM the new CNC.
The customer asked to be shown the new CNC software and how it links to CAD/CAM. ONA uses both software systems to obtain the best matching, so that the “ideal” part created by CAD/CAM software is processed by the machine’s CNC and the final result is an exact replica of what was designed. In this particular case, it was very important to pinpoint the holes that had already been drilled, to determine the exact coordinates in real time and ensure that the machine was able to perform the operation at the exact spot. The set-up of the workpiece was crucial, as well as being able to position it at the exact point, as the shape of the parts was very complex.
-
Programming with ONA Script.
Finally, programming was carried out using our ONA Script software tool, a workflow generator enabling the machine to seamlessly execute the whole process.
In the case of this particular task, it was a turnkey project involving a high level of collaboration with the customer at all times. This made it easier to successfully reach the end goal of directly manufacturing a part.
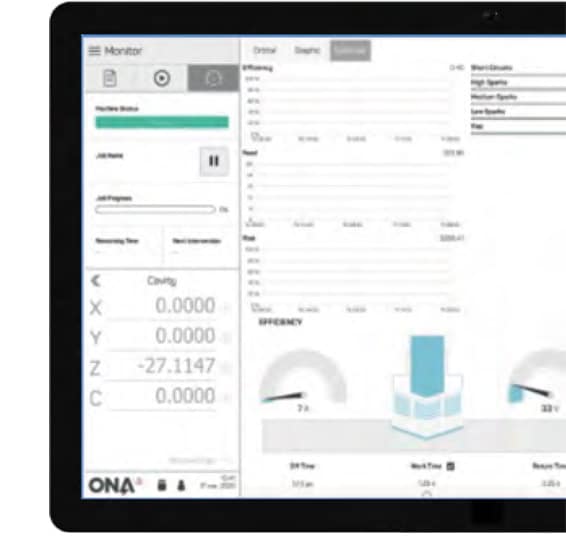
Conclusions
As a result of all this hard work and previous studies, we were able to provide the customer with a fully customised die sinking EDM machine programmed according to their specific needs for the machining of diffuser holes with complex geometry in turbine blades. As the customer informed us, our turnkey solution was also more cost-effective than other alternatives on the market.
The ONA IRIS6 machine incorporates a smart digital generator, a game-changing technological innovation in EDM technology. It is 30% more powerful than other more advanced generators. It can reach up to 400 amps, four times more powerful than the standard generator, and is designed to optimise the die sinking EDM process by controlling the energy input of each discharge, thereby reducing electrode wear by up to 500%.
The most important aeronautical companies in the world already use ONA machines in their processes, and our objective is to continue innovating and expanding in an industry in which EDM is going to play an increasingly important role. While not so long ago only a few applications were manufactured using EDM technology, nowadays, thanks to the major technological breakthrough brought by the new digital generators, electrical discharge machining has now become the technological norm for manufacturing vital parts such as impellers, IBRs, OGVs, turbine discs or combustion chambers, among others. otras.