At ONA we are experts in custom automated solutions in EDM, a big competitive advantage for our customers. Workpieces with a perfect finish in less time at a lower cost.
\ Automated solutions in EDM Machining: a big competitive advantage
As leader in EDM technology, ONA is referenced worldwide for the development of customized projects to suit the particular requirements of each client. It analyzes what the client needs and offers state-of-the-art automation solutions to optimize production processes in each case and makes the best possible use of the machine for its entire useful life. Workpieces with a perfect finish in less time at a lower cost.
Its 65 years as experts in EDM have helped ONA to develop a great capacity for undertaking automation projects. It carries out a preliminary in-depth study of each client’s requirements in order to subsequently design the customized automated machine. All this allows for a more intuitive handling of the machine with automated applications, electrode changing without machine downtime, complete processes for the manufacturing of molds without interruption. ONA can thus guarantee the maximum number of machine working hours without breaks, and get the best out of each production process.
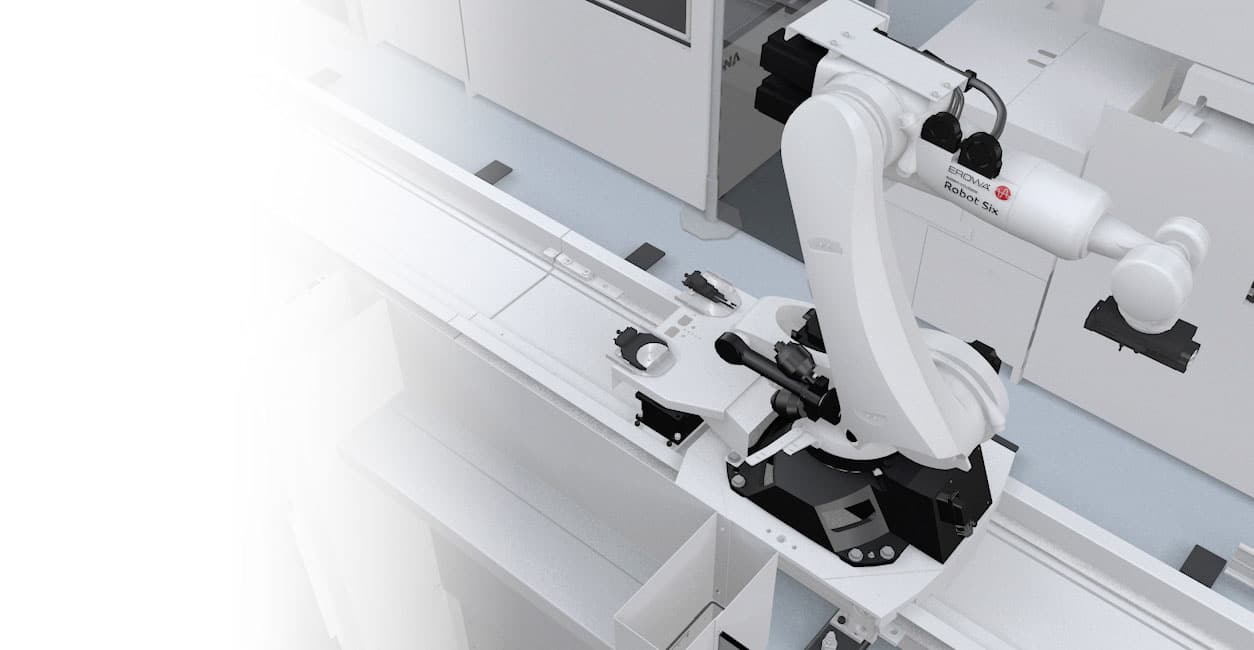
A wide range of automated processes. Great added value
As part of its policy of delivering great differentiating added value as a competitive edge, ONA offers a wide range of automation solutions integrated in the machine:
An extensive array of automatic changers developed by ONA that guarantee maximum performance according to each client’s needs.
- Linear changers integrated in the machine.
- 20-position automatic changer integrated in the machine.
- 40-position automatic changer ready for its adaptation to any model of machine.
In addition, it makes special changers for large or heavy electrodes.
Multi-electrode robots
Which can work with a single machine or integrate several EDM machines, or machining and EDM machines. The robot affords the machine great autonomy and ensures a more efficient use of time.
Integration of two multi-electrode robots in double head machines
ONA offers the possibility of including a second head in its catalogue of machines. This technological improvement shortens erosion time by 50% and it raises productivity by up to 200%. Half the time to get the same results in an automated process with the possibility of integrating two robots. For example, ONA is presenting its TQX10 model with double head and two multi-electrode robots and management software.
Development of personalized software
As part of its philosophy of personalization, ONA develops applications and control software adapted to each client’s needs. Its machines include process control software to manage the plant’s manufacturing status at any given time. Each integrated software accesses different programs for them to be run easily. The entire flow of information relating to the machining of workpieces is stored digitally, to avoid the loss of data as well as errors.
Manufacturing cells
ONA offers an integral automation service to all its clients to assist them in improving their working process, with the option to integrate flexible manufacturing cells. As a result, the entire electrode charge process can be automated, as can the manufacturing process, from the palletized pieces to the accessories. Additionally, manufacturing priorities can be modified halfway through the process.
25 years’ experience in automation
ONA experience in process automation is backed up by its 25 years researching and developing increased autonomous models which are constantly adapted to meet the increasingly competitive demands of the EDM sector. Since 1992, ONA has invested technology in projects designed to be automated as well as fully integrable in production cells. In addition, it has developed different product integration projects. ONA offers a complete manufacturing solution for all kinds of users, with top quality results without the need for an expert. It allows for remote control from another room away from the factory floor, thus avoiding having to work near the machine or the human errors in the production of the workpieces. Its machines are designed to get the best performance, to optimize processes and times and to guarantee a perfect result from start to finish. In addition, it generates a flow of precise information in real time on how each piece is made and the time it takes to make it.