Maximum productivity with ONA TQX10: the market’s largest twin head EDM model for the USA’s automotive and turbine sector
There are already more than 15,000 ONA machines installed in major automotive and turbine manufacturing companies around the world.
\ Maximum productivity with the ONA TQX10 twin head EDM machine
\ Concours Mold is a direct supplier to companies such as General Motors, Ford, Nissan, Chrysler, Tesla, Toyota, Volkswagen, BMW, and Mercedes-Benz.
\ ONA’s TQX10 double head machine makes it possible to save 50% of the erosion time, and increase productivity by 200%.
\ ONA EDM for one of North America”s leading automotive mold manufacturers
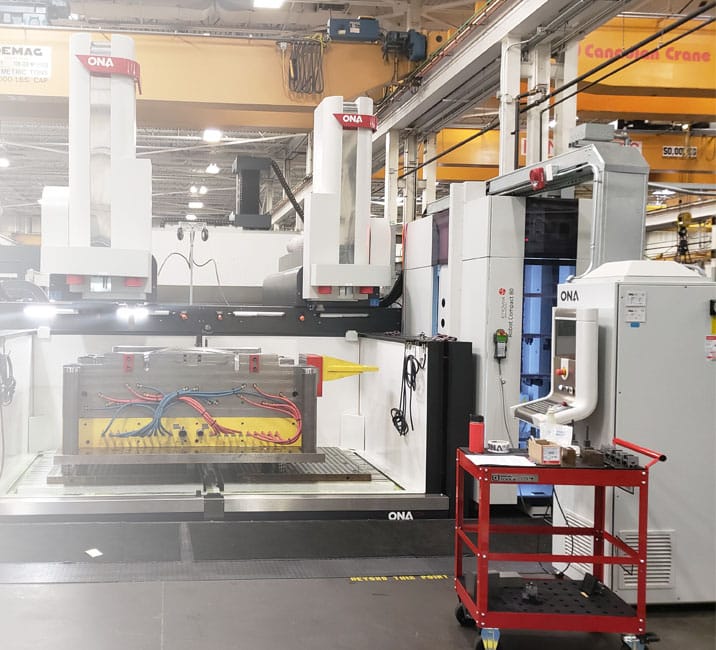
For more than 65 years, ONA has been focused on EDM, developing excellent quality solutions for the production of highly accurate and reliable molds and parts.
There are already more than 15,000 ONA machines installed in major automotive and turbine manufacturing companies around the world. One of such companies is Concours Mold, which is one of the leading manufacturers of large automotive molds in North America. Headquartered in Ontario (Canada), it also has plants in Mexico and in the United States, and is the direct supplier to General Motors, Ford, Nissan, Chrysler, Tesla, Toyota, Volkswagen, BMW, and Mercedes-Benz.
In order to provide a reliable response and the best possible service to such important companies, last year, Concours Mold acquired the double head ONA TQX10 die-sink EDM machine, which is the biggest in the market.
It was not the first time that Concours Mold used ONA technology to manufacture its molds. It has been our client for a quarter of a century now and, before acquiring the TQX10, it already had 2 ONA machines, with double head too: A THS700 (2004) and a TQX8 B1L (2014).
\ Erosion test to compare qualities
Before acquiring the TQX10, and despite being “very satisfied” with the performance of the 2 ONA EDMs already operating in their facilities, Concours Mold wanted to perform a test with other competing equipment to “compare options”. The result of the test was that our technology provided them with “better performance” both in terms of productivity and in the final quality of the molds.
Ed Ergun, Sales Manager at the Canadian company, stated: “We are always looking for the latest breakthrough in machinery and equipment. We are willing to test and implement it, if that results in a more agile manufacturing process, better quality parts and shorter lead times for our clients.”
Having EDM machines, such as the one ONA provides, makes it possible for Concours Mold engineers to achieve their demanding quality goals for molds, as well as to rigorously fulfill the established delivery times, between 8 and 24 weeks, depending on the mold size and on its technical complexity. The company can manufacture between 300 to 350 molds per year.
\ Double head EDM
Concours Mold was clear that its new EDM needed to have a double head, something that can be accomplished by very few manufacturers in the world. ONA was one of the first to develop this technology, more than two decades ago.
Combining these 2 heads simultaneously and independently saves 50% of the erosion time and increases productivity by 200%. The TQX10 equipment purchased by Concours Mold also includes 2 EROWA robots for changing electrodes on the sides, which avoids machine downtime, and enables the mold production to be fully automated.
One of the main advantages of this model is that it can be used as 2 independent machines by separating the tank. However, it can also be used jointly as a single machine, but with double head. In the latter case, both heads communicate with each other to control erosion zones and increase productivity.
They are especially useful models for the manufacture of large molds and different cavities, the specialty of Concours Mold.
Some improvements we have recently made in ONA’s double head EDM models are:The distance between heads can be modified according to specifications.
- Vertical extension with automatic double changer. Two chucks are fitted on the C-axis and at the end of the extension. This makes it possible to optimize the use of extension electrodes, and to erode at a greater distance without colliding with the head.
- Automatic adjustment of the dielectric level, maintaining it at the level of the head.
- Its software is specially designed for double-headed equipment, which facilitates managing the performance of both machines.
At ONA, we offer companies the possibility of configuring machines according to their specific needs. In addition, we have more than 70 modular setups, for both die-sink and wire-cut EDM, with delivery times similar to those of a standard model and without additional charges.
Simply Contact, and let us know what you need. We’ll take care of the rest.